Fluorite ore is a vital industrial mineral widely used in metallurgy, chemical, and ceramic industries. Depending on the gangue minerals present, fluorite ore can be classified into quartz-type, calcite-type, barite-type, and sulfide-type. Currently, the main fluorite processing methods for fluorite ore are gravity separation and flotation, with flotation being the preferred method for fine-grained fluorite ore and acid-grade fluorite concentrate.
1. Cost Composition of Flotation Process
The flotation process involves altering the surface properties of minerals by adding flotation reagents to achieve separation. In the daily operation of a flotation plant, various factors such as equipment, materials, energy, labor, and management contribute to production costs, which must be comprehensively considered during cost calculations.
1.1 Equipment Costs
The fluorite ore flotation process includes stages like crushing and screening, grinding and classification, flotation, drying, etc. Major equipment includes jaw crushers, ball mills, spiral classifiers, flotation machines, thickener,Filter press, feeders, and conveyors. The investment costs for these pieces of equipment are high, covering the expenses of purchase and installation.
1.2 Flotation Reagent Costs
Flotation reagents play a crucial role in the flotation process. The type and consumption of reagents vary with the ore type. Common reagents include:
*Quartz-type fluorite ore: sodium carbonate (modifier), fatty acids (collector), and sodium silicate (quartz depressant).
*Calcite-type fluorite ore: pH adjustment with sodium silicate, sodium hexametaphosphate, etc., as depressants.
*Barite-type fluorite ore: fatty acid flotation reagents combined with organic depressants like dextrin and caustic starch.
1.3 Electricity Costs
A variety of equipment in the processing plant requires electricity for operation, including crushing and grinding.
1.4 Equipment Maintenance and Repair Costs
Routine maintenance includes small consumables (e.g., oil, filter cloth) and repairs of major equipment (e.g., ball mill liners, flotation machine impellers). Maintenance and repair costs and replacement cycles must be considered.
1.5 Labor Costs
Despite the presence of automated management systems, skilled workers and technical personnel are needed to operate the equipment and monitor the process to ensure stable production.
1.6 Other Costs
In addition to the main costs, daily operating expenses such as analysis, transportation, packaging, and wastewater treatment must also be considered. These expenses also impact the overall cost.
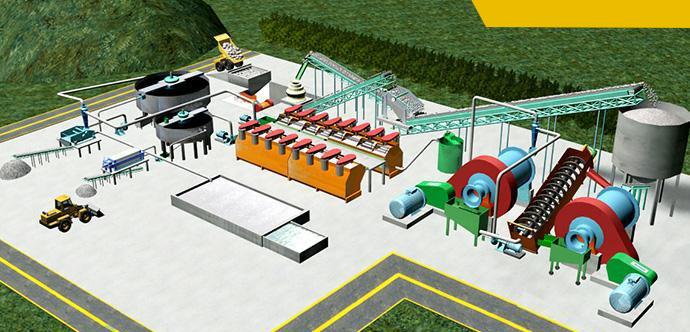
2. Production Cost Analysis of the Flotation Plant
Assuming a processing plant with a capacity of 200 T/H, processing quartz-fluorite ore with CaF₂ grade of 50%, the equipment and production costs are estimated as follows:
2.1 Equipment Costs:
Major equipment includes: crusher*2, ball mill*1, spiral classifier*1, 20-40 sets flotation machines, thickener*1, 2 filter presses*1, wastewater treatment equipment, conveyors, etc. The equipment cost is approximately 4-6 hundred thousand US dollars (excluding construction investment).
2.2 Flotation Reagent Costs:$300USD/Day
Reagents include fatty acids, sodium carbonate, and sodium silicate, with a daily consumption of about 460kg. The reagent cost is approximately $300USD/day
2.3 Electricity Costs: $1165USD/Day
With a total power of 400KW for the flotation plant and an electricity cost of 0.85 yuan per kWh, the electricity cost is $1165USD/day
2.4 Equipment Maintenance and Repair Costs: $741USD/Day
Cost for small consumables: $56USD/day
Repair costs for major equipment (e.g., ball mill liners, flotation machine impellers): $685USD/day (calculated based on an average cost with replacement cycles ranging from 1 to 8 months).
Total maintenance and repair costs: $741USD/day
2.5 Labor Costs: $457USD/day
With an automated management system in place and a 3-shift rotation, the labor cost for workers, technicians, and management is $457USD/day
2.6 Other Costs: $486USD/Day
Costs for analysis, transportation, packaging, and wastewater treatment: $486USD/day
2.7 Summary of Operating Costs:
Based on the above cost data, the daily production operating cost is $3149USD/day
Reagents + Electricity + Equipment Maintenance + Labor + Other
=300 + 1165 + 741 + 457+ 486
= $3149USD/day
Assuming a daily production of 80 tons of concentrate, the production cost per ton of fluorite concentrate is $40USD/ton
3. Conclusion
The production cost of a fluorite flotation plant is closely related to equipment, flotation process, and ore type. For different types, grades, and applications of fluorite ore, it is necessary to conduct tests and experiments to determine the most suitable flotation process and equipment configuration to achieve cost control and maximize benefits.