1. Calcite-Fluorite Ore
Calcite-fluorite ores primarily consist of fluorite and calcite (with calcite content often exceeding 30%), with minor amounts of quartz, forming quartz-calcite-fluorite ores. Due to the similar surface physicochemical properties of calcite and fluorite, which are both calcium-containing minerals, mutual transformation between these minerals can occur when they coexist in solution, making separation difficult. Therefore, the flotation of fluorite with a high calcium carbonate content is relatively difficult.
2. Flotation Reagents
Although the flotation separation of calcite and fluorite is challenging, it can be achieved by adjusting the pulp pH and using inhibitors such as sodium silicate, salted sodium silicate, acidified sodium silicate, sodium hexametaphosphate, lignosulfonate, dextrin, tannin, and tannic acid, either individually or in combination, to suppress calcite. Oleic acid or other fatty acids are used as collectors for fluorite to achieve the separation of calcite and fluorite.
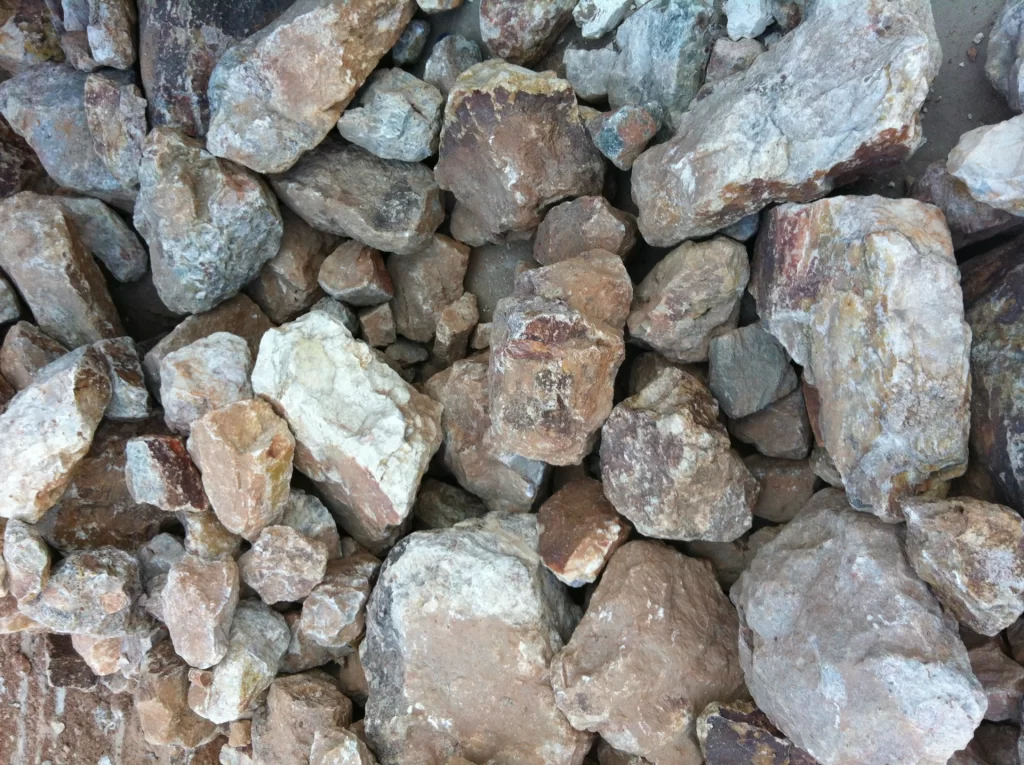
3. Flotation Process
The calcite (calcium carbonate) and fluorite beneficiation process involves the following steps:
1. The ore sample is first ground or directly selected if it meets the required particle size.
2. Roughing: Oleic acid or saponified oleic acid is used as a collector, hydrochloric acid as a pH regulator, and acidified sodium silicate as a calcium carbonate inhibitor. The flotation roughing treatment is conducted with the flotation pH value adjusted to a range of 5-7.
3. Cleaning: Hydrochloric acid is again used as a pH regulator, and acidified sodium silicate as a calcium carbonate inhibitor. The roughened ore slurry undergoes at least three cleaning stages, with the pH value during cleaning controlled within the range of 5-7. This completes the separation of fluorite from calcium carbonate through flotation.
4. Conclusion
In summary, to achieve the flotation separation of fluorite and calcium carbonate, both a reasonable fluorite flotation technology and effective flotation reagents are required. This ensures both high-quality fluorite concentrates and high recovery rates.
The flotation process and reagent selection for fluorite ore require experimentation to determine. The flotation treatment line for fluorite ore also varies and needs to be designed based on the mineral properties.
Forui Machinery is a professional manufacturer of beneficiation equipment. Our factory has designed fluorite beneficiation technology and equipment configuration for multiple fluorite beneficiation plants and has a complete test platform. It can conduct beneficiation tests and design processes for customers.
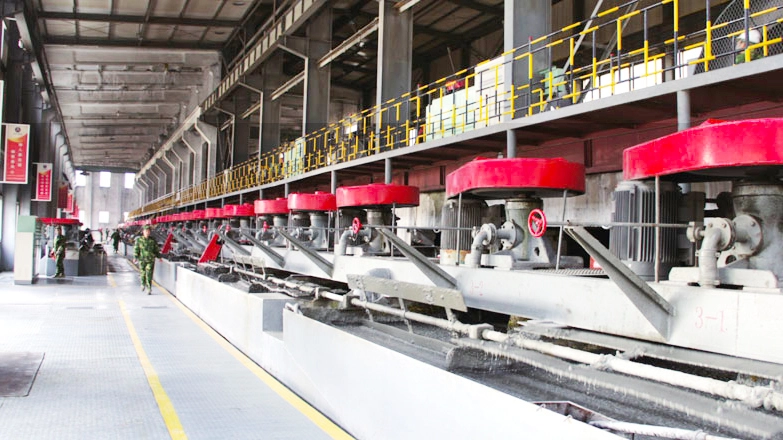
Kathy Niu
Email: Kathy.niu@foruimining.com
support@foruimining.com
WhatsApp: +8618838083794
Henan Forui Machinery Technology Co.,Ltd
What is the Beneficiation Process of Fluorite Ore
Fluorite Flotation 01:Sulfide–Fluorite Ore
Fluorite Flotation 02:Barite-Fluorite Ore
Fluorite Flotation 03:Quartz-Fluorite Ore
Can the Low-grade Fluorite be Enriched by Gravity Beneficiation?
How to Improve the Grade of Fluorite by Using Gravity Dressing Process