Flotation plant equipment plays a pivotal role in mineral processing, directly impacting ore recovery rates and concentrate grades. A well-structured maintenance and optimization strategy not only reduces equipment failures but also significantly improves operational efficiency and stability. This article explores specific measures that can be implemented based on practical maintenance tasks, focusing on equipment maintenance, lubrication management, and optimization strategies to ensure the long-term stable operation of flotation plants.
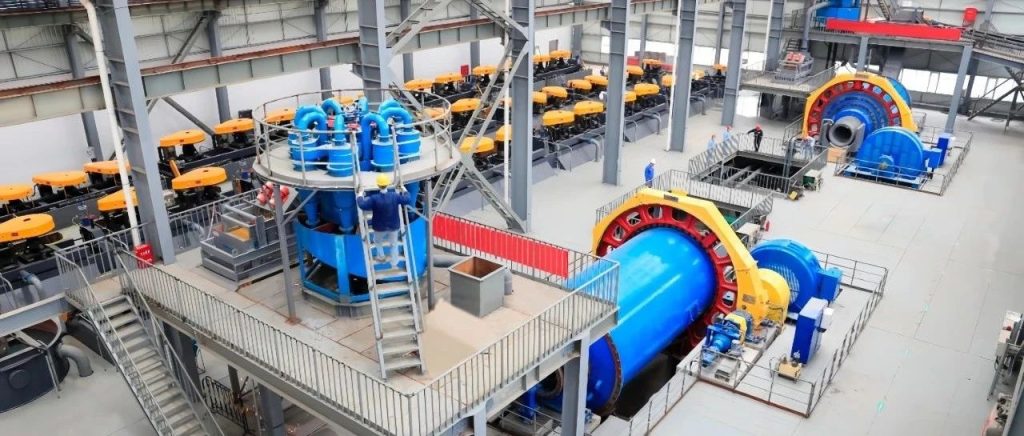
01 Equipment Maintenance
Regular inspection and maintenance are essential for ensuring the continuous and stable operation of mineral processing equipment. These practices prevent breakdowns, reduce downtime, and effectively extend equipment life, thereby lowering maintenance costs
1.1 Regular Inspection and Maintenance
Regular inspections help identify potential equipment problems and prevent minor issues from escalating into major failures. Common maintenance tasks include:
*Replacing ball mill liners and end caps: Liners and end caps are critical components of ball mills. Prolonged wear can affect mill stability. Regular replacement reduces excessive wear on mill bearings and other important components.
*Inspecting large gear rings and mill base foot bolts: Regular inspection and adjustment of large gear rings and foot bolts ensure smooth mill operation and prevent equipment failure caused by loose bolts.
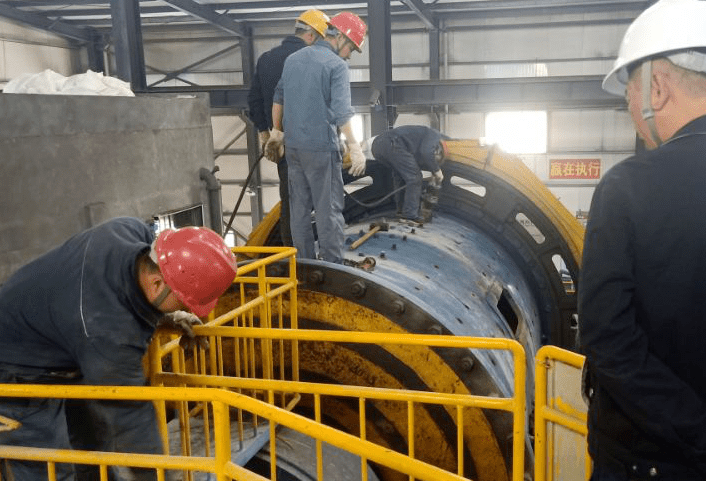
*Replacing classifier frames and blades: Over time, classifier frames and blades can affect classification efficiency. Timely replacement ensures efficient classification and avoids affecting subsequent processing stages.
*Maintaining flotation pumps: Regular inspection of oil seals, packing boxes, and water seals of flotation pumps prevents instability in flotation and affects concentrate recovery.
After each maintenance activity, data on equipment workload, component wear, and other relevant factors should be recorded for reference in future maintenance and optimization.
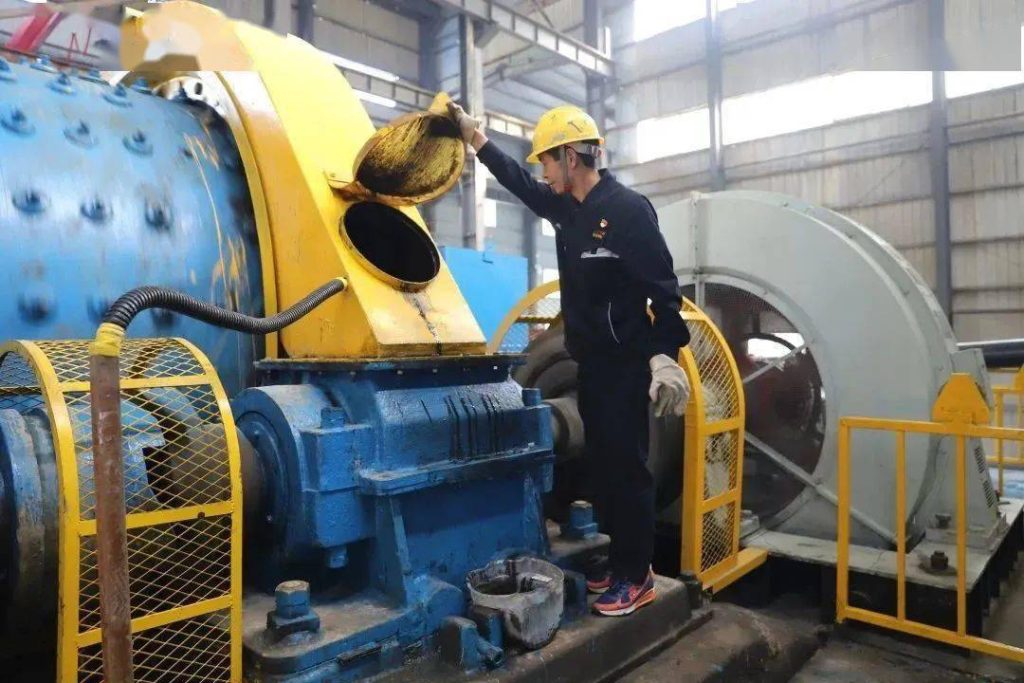
02. Lubrication Management
For mineral processing equipment, lubrication not only reduces wear but also provides cooling, cleaning, and rust prevention, extending equipment life. Lubrication system management involves several aspects:
*Regularly checking the condition of lubricating oil: The quality of lubricating oil directly affects equipment operating efficiency. The condition of lubricating oil should be checked regularly, and old oil should be replenished or replaced in a timely manner.
*Ensuring the unobstructed flow of lubricant to lubricated parts: For all lubricated parts, ensure that the lubricant flows smoothly to prevent oil pipe blockage and equipment wear or overheating.
*Monitoring lubricant temperature: For high-load components such as bearings, if the temperature exceeds the set standard (e.g., 55°C), cooling measures should be taken or the lubricant flow rate increased.
*Inspecting and maintaining the lubrication system: Regularly inspect and replace oil seals, packing boxes, and other components in the lubrication system to prevent deterioration or wear and reduce lubrication effectiveness.
*Upgrading the lubrication system: For long-term equipment, consider using more efficient lubricants or upgrading the lubrication system to further improve lubrication performance and operational stability.
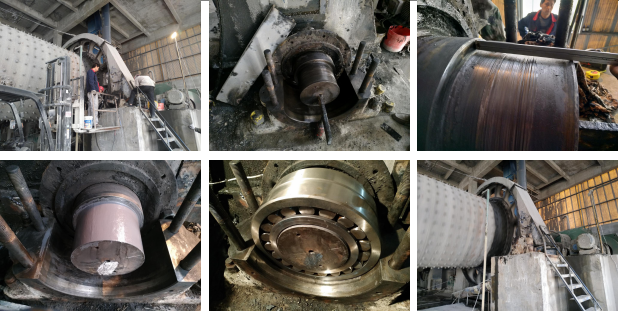
03. Equipment Optimization
Equipment optimization can significantly improve the production capacity of mineral processing equipment, reduce energy consumption, and enhance mineral processing efficiency. Equipment modifications, upgrades, and adjustments to operating parameters can significantly improve equipment operating efficiency and stability.
3.1 Equipment Modification and Upgrades
Equipment modification and upgrades are essential aspects of equipment optimization. By modifying and upgrading equipment, performance and reliability can be improved.
*Replace inefficient motors with high-efficiency energy-saving motors and optimize the electrical control system to reduce energy consumption and improve operating efficiency.
*Replace old equipment to enhance automation control and reduce failures caused by human error.
*Improve equipment design to reduce wear and energy consumption, ensuring long-term stable operation.
*Adjust grinding operation parameters based on ball mill wear to optimize equipment configuration and improve grinding efficiency.
*Based on daily maintenance records, optimize the use of flotation pumps in the flotation process to reduce the impact of slurry on equipment and extend service life.
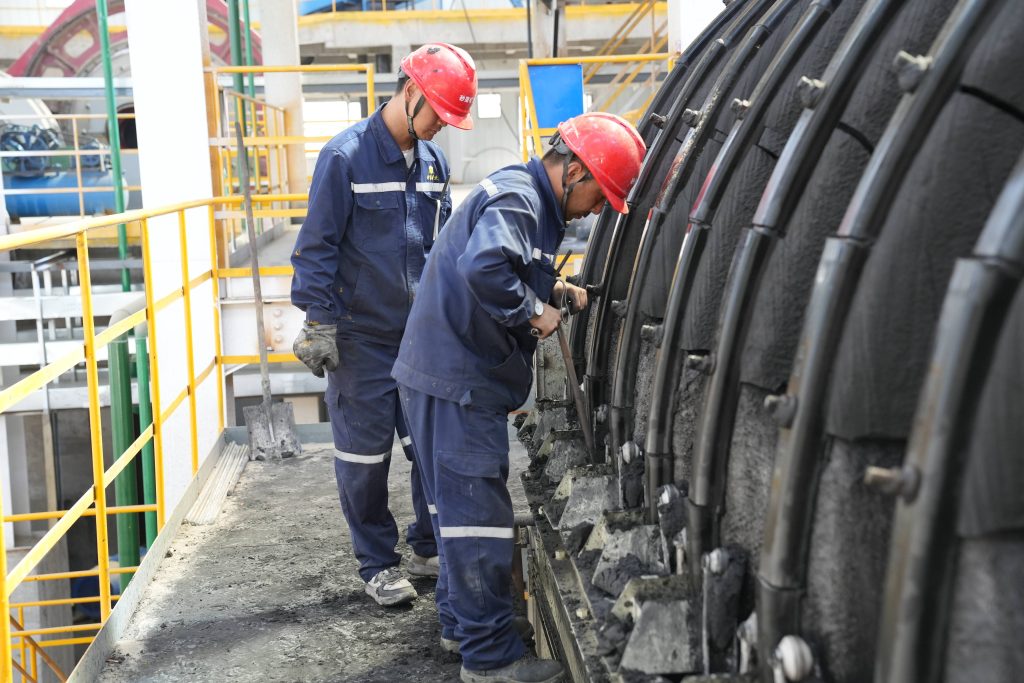
3.2 Adjustment of Operating Paramete
Equipment operating parameters directly affect mineral processing results. In actual operation, the equipment status should be monitored in real-time, and key parameters such as speed, feed rate, and discharge rate should be adjusted accordingly. Optimizing operating parameters not only prevents equipment overload but also improves production efficiency and extends equipment life. Using data-driven adjustment methods can ensure that the equipment always operates in the best state and reduce the risk of damage caused by improper operation.
Conclusion
A scientific maintenance and optimization strategy for flotation plant equipment is crucial for improving mining production efficiency, extending equipment life, and reducing failure rates. By implementing regular inspection and maintenance, lubrication management, equipment modification, process optimization, and adjustment of operating parameters, it can be ensured that the equipment operates efficiently while bringing higher economic benefits to the flotation plant.