Mineral processing relies on a variety of machine. It includes crushers (such as jaw crushers and cone crushers), vibrating screen, gravity separation equipment (like jig machine and shaking tables), flotation machines, magnetic separators, dewatering equipment (such as filter presses and cyclones), and conveyors. These mineral processing machines are vital for transforming raw ore into valuable products. Efficiently operating this equipment is crucial for the success of any mining operation.
However, maintaining mineral processing machine on a limited budget presents significant challenges. This article explores strategies to maximize equipment uptime while minimizing costs.
1. Prioritize Cost-Effective Machine Selection
When budgeting for mineral processing machine, prioritize cost-effectiveness. For critical items like crushers, focus on performance and the durability of parts during purchase. Despite higher upfront costs, these crushers have a longer life and lower failure rates, which decreases replacement and maintenance needs in the long run, saving costs in mineral processing operations.
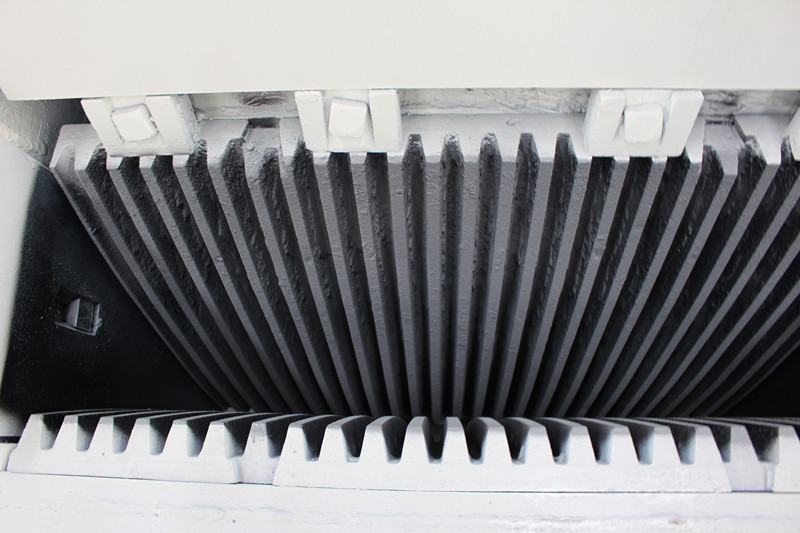
2. Implement a Robust Maintenance Plan
In situations with limited funds, developing a detailed and practical maintenance plan is vital. For instance, with a jaw crusher in mineral processing, it’s essential to regularly inspect the liner and the movable jaw for wear and replace parts showing significant wear promptly. By planning maintenance in advanced, one can prevent unexpected breakdowns that lead to costly repairs, thereby saving on costs.
3. Invest in Operator Training
When budgets are tight, comprehensive training for equipment operators is key to reducing maintenance costs. They should learn basic maintenance knowledge and skills of the mineral processing machine. For example, with flotation machines in mineral processing, operators should know how to adjust reagent dosages and bubble size for optimal flotation results and to minimize equipment wear and failure rates. Although training costs are relatively low, they significantly reduce repair and downtime costs caused by operator errors.
4. Embrace Preventive Maintenance
In budget-constrained scenarios, preventive maintenance for the mineral processing machine helps detect and address potential issues early, preventing unexpected shutdowns. For instance, regular checks and replacements of the wear-resistant liners on the spiral shaft of spiral classifiers in a mineral processing plant can avert shutdowns due to wear. This practice extends equipment life and reduces frequent repair costs.
5. Leverage Affordable Monitoring Technologies
On a tight budget, incorporating cost-effective monitoring tools can provide real-time equipment oversight. For example, using a portable vibration analyzer or a handheld infrared thermometer to monitor the operation of a cone crusher can warn of abnormal wear in bearings or drive components, allowing for timely intervention. These handheld devices are cost-effective, easy to operate, and can significantly reduce unplanned downtime and repair costs.
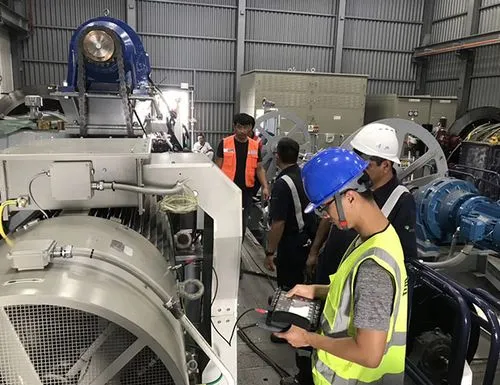
6. Optimize Production Schedules
With limited funds, proper production planning to avoid prolonged high-load operation of the mineral processing machine can decrease wear and failure rates. By optimizing production processes, such as managing the use of conveyors to avoid continuous operation for extended periods, equipment wear can be reduced, extending its lifespan. This minimizes production interruptions and repair costs due to equipment failures.
Conclusion
By strategically combining equipment selection, maintenance planning, operator training, preventive measures, technology, and production optimization, mineral processing plants can significantly enhance equipment uptime and reduce operational costs. This holistic approach ensures the long-term efficiency and profitability of mining operations.
Maintenance of mineral processing equipment is crucial to the efficiency of mining operations. Forui Machinery has dedicated 30 years to the research and development of beneficiation equipment. We not only offer customized beneficiation solutions and high-quality equipment, but also provide a comprehensive after-sales service system, including equipment installation, debugging, and spare parts supply.
Choosing us means selecting a reliable and worry-free partner. If you have questions about mineral processing, contact us
Henan Forui Machinery Technology Co.,Ltd
Email: kathy.niu@foruimining.com
support@foruimining.com
WhatsApp: +8618838083794
Your reliable mineral processing expert.
How to reduce downtime of Mineral Processing equipment?
Ore Washer Maintenance: Spiral Washers, Log Washer, Rotary Scrubber