1. Quartz-fluorite Flotation Process
Quartz is the primary gangue mineral in quartz-fluorite ores, where the fluorite content is relatively high, reaching up to 80%. A common fluorite flotation processing flow involves coarse grinding followed by one stage of rougher flotation, then regrinding the rough concentrate and performing multiple stages of cleaner flotation.
In the quartz-fluorite flotation, sodium carbonate (Na2CO3) is commonly used as a pH regulator, with fatty acids acting as fluorite collectors, and sodium silicate is applied as a quartz depressant. The typical pH of the pulp is maintained at 8-9. The reagent usage process is as follows: Sodium carbonate (Na2CO3) adjusts the pulp to an alkaline condition to prevent quartz activation by multivalent cations in water. Fatty acids are applied as collectors, and an appropriate amount of sodium silicate is added to inhibit silicate gangue minerals. The dosage of sodium silicate must be carefully controlled because a small amount can activate fluorite, while an excessive amount can inhibit it.
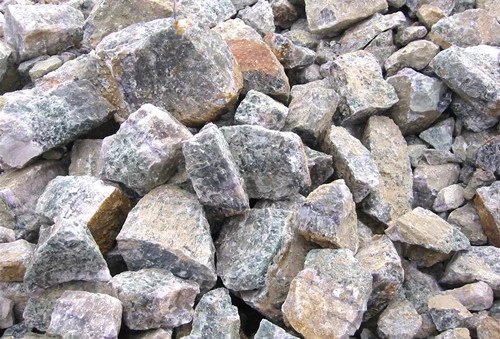
2. Flotation Cases
2.1 Fluorite Ore Grade
Expert Wang Zengzai floated and purified a quartz-fluorite ore from Jiangxi using petroleum sulfonate as a collector and sodium silicate as a depressant through a process of “1 grinding, 1 rougher and 4 cleanings”. The obtained fluorite concentrate had a CaF2 grade of 97.45% and a recovery rate of 89.54%.
2.1.2 Low-grade Fluorite Ore
For low-grade quartz-fluorite ores, expert Li Jifu regulated the pH with sodium carbonate and used sodium silicate as a depressant, along with an anionic fatty acid collector K-410, to float and purify fluorite ore containing 21.55% CaF2. A closed-circuit flotation process of “1 rougher, 6 cleaners, and 2 scavengers” yielded a fluorite concentrate with a CaF2 grade of 95.37% and a recovery rate of 85.82%.
Due to the disadvantages of oleic acid collectors, such as poor selectivity, poor low-temperature resistance, and poor solubility, many researchers have developed new collectors with excellent performance.
Expert Deng Haibo used a self-developed new low-temperature collector DW-1 for a quartz-fluorite ore with an original CaF2 grade of 17.32%. In a low-temperature environment of 6°C, a flotation process of “1 rougher, 1 scavenger, and 6 cleaners, with intermediate products sequentially returned” was applied to obtain a fluorite concentrate with a CaF2 grade of 98.37% and a recovery rate of 80.12%. The flotation effect was better than sodium oleate, and the reagent dosage was lower.
Expert Zhang Xiaofeng used ZYM, an independently developed collector, for low-temperature flotation of fluorite. At a pulp temperature of 5-10°C, the obtained concentrate had a CaF2 grade of 97.55%, a SiO2 grade of 1.36%, and a fluorite recovery rate of 76.67%.
2.2 According to the grain size distribution
Based on the grain size distribution of valuable minerals, quartz-fluorite ores can be mainly divided into coarse-grained and fine-grained types, each requiring a different flotation separation process.
For coarse-grained ores: Fatty acid collectors are commonly used, sodium carbonate is used as a pulp regulator, and sodium silicate is applied as a quartz depressant. A simple process of one rougher and multiple cleaners can yield high-quality fluorite concentrate.
For fine-grained ores: The flotation reagents are the same as those for coarse-grained quartz-fluorite ores, but due to the finer grain size of the target mineral, more intense grinding is required, and a stagewise grinding and stagewise selection process is adopted.
3. Conclusion
Overall, the flotation process for quartz-fluorite ores is mature, the separation process is simple, and the flotation index is good. The development of low-temperature and high-efficiency collectors is the current focus of research on quartz-fluorite ore flotation.
The flotation process and reagent selection for fluorite ore require experimentation to determine. The flotation treatment line for fluorite ore also varies and needs to be designed based on the mineral properties.
Forui Machinery is a professional manufacturer of beneficiation equipment. Our factory has designed fluorite beneficiation technology and equipment configuration for multiple fluorite beneficiation plants and has a complete test platform. It can conduct beneficiation tests and design processes for customers.
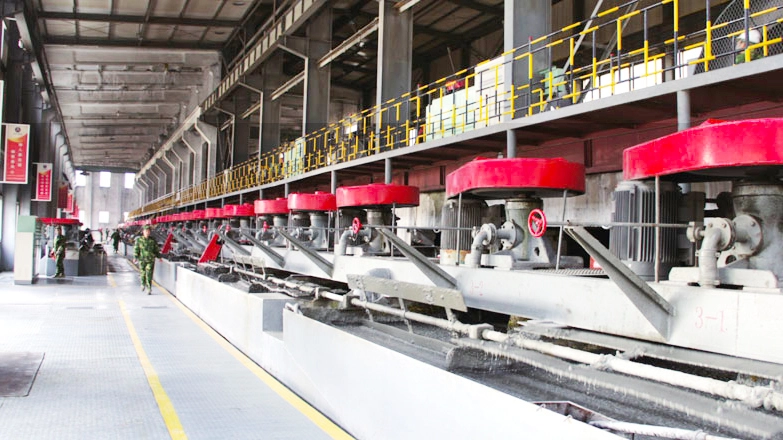
Kathy Niu
Email: Kathy.niu@foruimining.com
support@foruimining.com
WhatsApp: +8618838083794
Henan Forui Machinery Technology Co.,Ltd
What is the Beneficiation Process of Fluorite Ore
Fluorite Flotation 01:Sulfide-Fluorite Ore Flotation
Fluorite Flotation 02:Barite-Fluorite Ore Flotation
Fluorite Ore Processing Flowsheet and Washing Plant
Can the Low-grade Fluorite be Enriched by Gravity Beneficiation?
How to Improve the Grade of Fluorite by Using Gravity Dressing Process