Ore washing is the process of using water or mechanical force to agitate and scrub raw ore, thereby separating clay and other impurities from the ore. Alluvial ore deposits, such as gold, platinum, tungsten, and tin, along with other minerals like lead, copper, iron, and manganese, undergo deep oxidation and weathering. Consequently, they necessitate this essential washing process. Through washing, we eliminate gangue or clay from these ores prior to crushing or beneficiation. This preliminary step enhances the efficiency and effectiveness of the subsequent processing stages.
1. Why Wash the Ore?
1.1. Preparation for Crushing: By washing away the mud on the ore, we can effectively reduce the clogging of crushers, thereby avoiding downtime and increasing overall efficiency.
1.2. Preventing Equipment Clogging: Ore washing can prevent bins, crushers, and screening equipment from clogging, thereby ensuring smooth operational flow.
1.3. Improving Beneficiation: Ore washing can improve the ore grade and increase recovery rates. For low-grade ores such as manganese, phosphate and iron ore, washing can increase the ore grade by 5-20%, which in turn boosts recovery rates in subsequent magnetic separation and flotation processes.
2. Clay Properties and Ore Washer Selection
The washability of ore is related to clay plasticity, water content, expansibility, permeability, and ore grain size composition.The more easily the clay washes out, the more effective the ore washing process becomes.
Difficulty of ore washing | Clay property | Clay plasticity(K) | Necessary Wash Time/ /min | Wash method |
Easy | Sandy clay | 1-7 | <5 | Vibrating screen, trommel screen |
Midium | Separable by fingers | 7-15 | 5-10 | Rotary scrubber, spiral washer |
Hard | Clay massed, not easily divisible by fingers | .15 | >10 | Log washer |
3. Types of Ore Washing Machines
Two primary types of ore washing processes exist: The use of ordinary screening machinery in conjunction with water forms one method among two primary types of ore washing processes, suited for ores of low clay content and low plasticity.
Another that utilizes specialized washing equipment necessary for ores with high clay content, high plasticity, and agglomeration. Such ores typically necessitate multiple washing cycles, often two or three, to achieve efficient clay separation.
3.1 Rotary scrubber
The rotary scrubber is suitable for cleaning non-sticky materials in ores, capable of handling material sizes up to 230mm with high processing capacity. Its cylinder barrel, lined with manganese steel or rubber, enhances material dispersion and movement. Moreover, high-pressure water guns are installed inside the drum. These guns blast the ore with high-pressure water streams, effectively removing surface impurities.
3.2 Log washer
The log washer is ideal for ores with sticky clay, handling material sizes up to 70mm. It offers strong scrubbing ability and high cleaning efficiency. Additionally, chemical agents such as a 1% concentration of NaOH can be added to enhance the cleaning power.
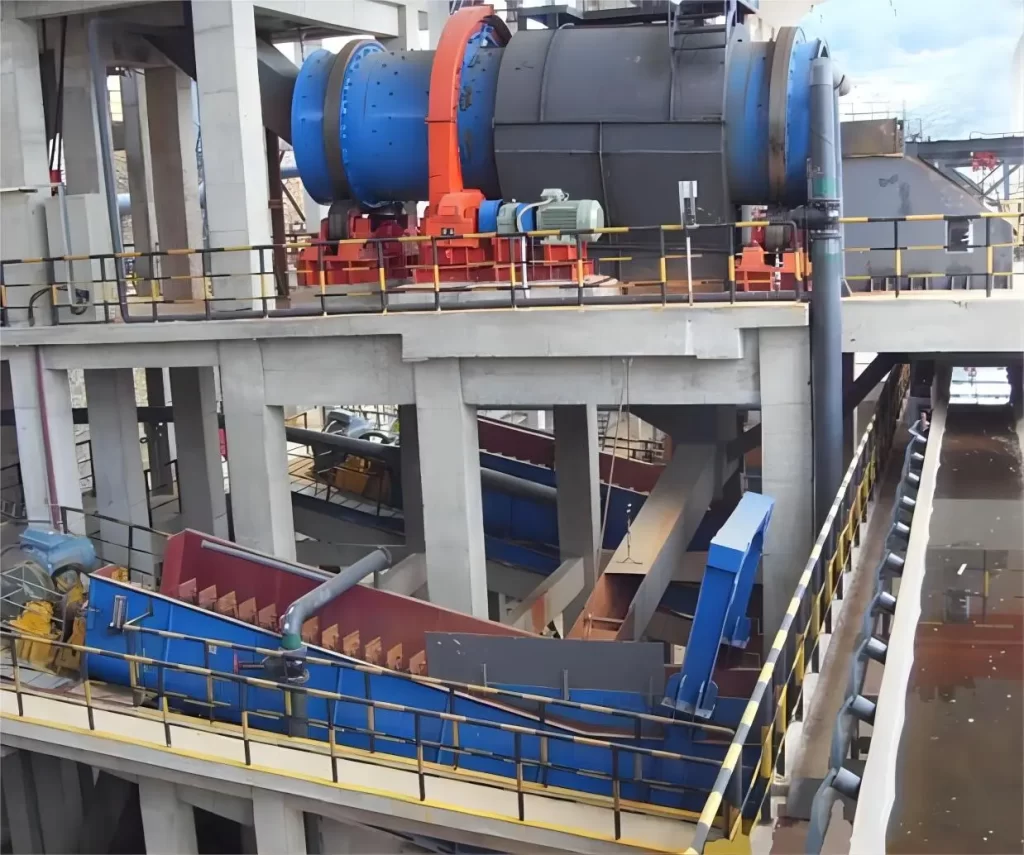
3.3 Spiral Washer (Fine Mineral Washer & Sand Washer)
The spiral washer, also recognized as a “fine mineral washer” or “sand washer”, excels at cleaning small-grained ores and sands. This equipment effectively enhances the purity of materials within the 10mm size range.
3.4 Vibrating Washing Screen
Designed specifically for materials with low soil adhesion, this vibrating washing screen employs a series of spray nozzles positioned above the screen deck. As the material moves across the screen, these nozzles continuously spray water, effectively removing surface soil. This efficient cleaning process enhances screening accuracy and product purity.
3.5 Trommel Screen
The trommel screen, designed for non-sticky soil and commonly used in gold sand washing and grading, is made from steel, woven mesh, or steel rods. It features a high-pressure flushing water pipe and operates at a rotation speed of 15-30r/min. Boasting a production capacity of 20-400t/h, it includes built-in impeding plates to enhance the washing effect.
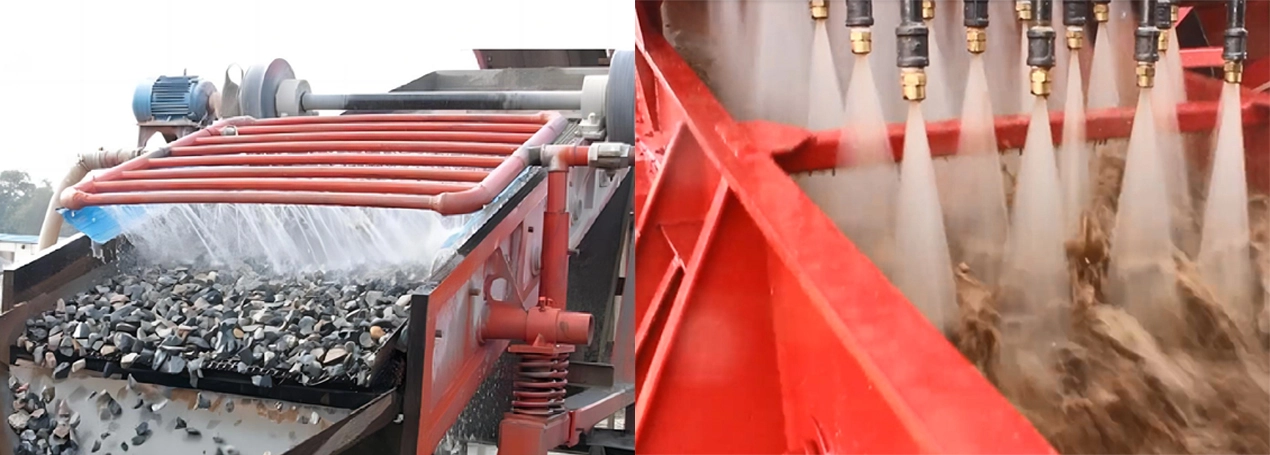
4. How to Choose Ore Washing Machine?
When selecting ore washing machines, consider the following factors:
4.1. Efficiency: High-efficiency washing functions are crucial for enhancing final product quality, reducing waste, and increasing profitability.
4.2. Capacity Matching: Ensure the washing equipment’s capacity aligns with production demands to prevent bottlenecks and maintain smooth operations.
4.3. Low Maintenance Costs: Opt for washing equipment with low maintenance and energy efficiency for long-term cost savings.
4.4 Reliability and Durability: The equipment’s reliability and durability are key to uninterrupted production.
4.5. Quality Service: Choose suppliers with a strong reputation and excellent after-sales service for prompt issue resolution and minimal downtime.
5. Need Help Choosing Ore Washers?
If you’re uncertain about how to select the right ore washers, contact us. FORUI Machine can customize the most suitable ore washing equipment based on your specific needs and mineral characteristics, offering efficient, reliable, and environmentally friendly ore washing solutions.
- Kathy.niu@foruimining.com
- support@foruimining.com
- WhatsApp: +8618838083794