Ore washer plays a pivotal role in the mining industry, ensuring both production efficiency and the quality of the ore. This comprehensive guide outlines the essential operational and maintenance pointers for various types of ore washing machines to assist users in maximizing the ore washers and longevity of these machines. Thus reducing downtime of washing and ensuring ore processing production efficiency
The mainly ore washing machines include rotary scrubbers, spiral washers( fine material washer ), log washers and vibrating washing screens. The trommel screen is also often used for washing alluvial gold, but it is not equipped with water sprays. Therefore, no narration will be made.
- Rotary scrubber
- Log washer
- Spiral washer
- Vibrating washing screen
1. Rotary Scrubber
The rotary scrubber utilizes a rotating drum to allow rocks to collide, rub, and tumble, combined with high-pressure water spray to wash away mud. Subsequently, the ore is graded and discharged through a rotary screen, while wastewater containing sludge is removed through a hole baffle at the feed end.
This type of ore washer is suitable for cleaning large pieces of ore, which size is more than 230mm
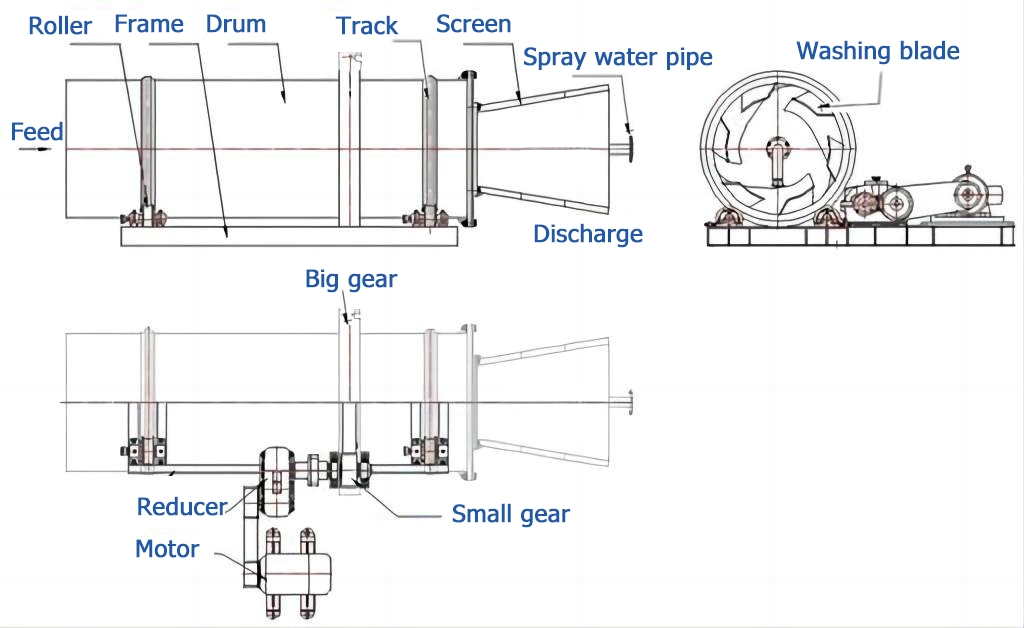
Operation Requirements:
1. Control the drum speed and filling rate to achieve the best washing results.
2. Monitor the feed and discharge ports to prevent blockages from oversized or undersized materials.
3. Maintain the correct amount of water spray for thorough ore cleaning.
Maintenance Requirements:
1 Bearings are critical. Ensuring clean, well-sealed lubricating oil at all main oil injection points, including rotating bearings, roller bearings, gears, and movable bearings and sliding surfaces.
2. Check newly installed wheel hoops regularly to prevent loosening.
3. Inspect the drum’s wear condition, especially at weld points, to prevent material leakage.
4. Maintain the spray system to ensure stable water pressure and flow.
2. Spiral Washer
Also known as a “sand washer” or “fine material washer,” the spiral washer is an efficient piece of equipment for cleaning fine ore particles.
The spiral washer uses the buoyancy of water to separate dust and impurities from the ore. Through theagitation of the spiral blades, the purpose of filtering water and removing impurities is achieved.
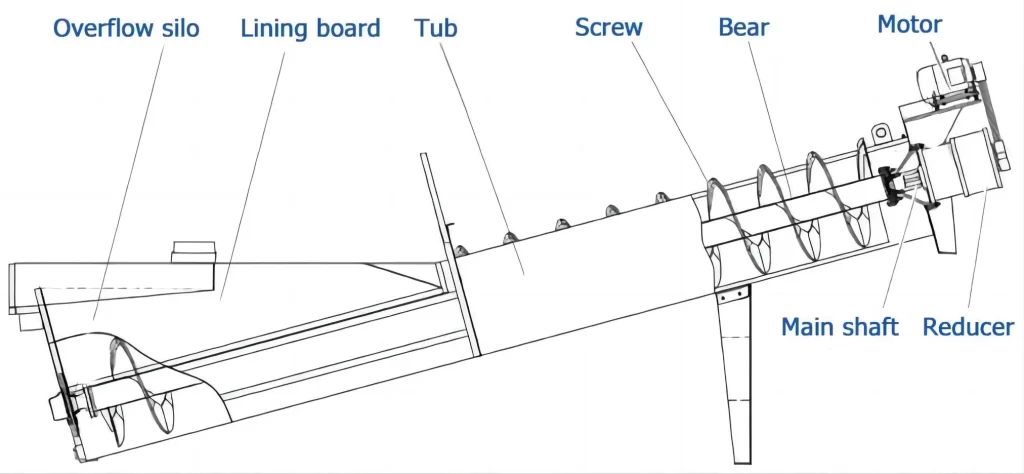
Operation Requirements:
1. Achieve uniform feeding to prevent overloading or underloading, which could impair the washing process.
2. Manage water flow and pressure to secure optimal washing outcomes without excessive water usage.
Maintenance Requirements:
1. Conduct regular inspections of bearing wear and replace them as needed. Remember to change the bearing lubricant every three months and clean the bearings with clean gasoline or kerosene.
2. Replace the oil, fuel, or antifreeze of the spiral sand washer seasonally.
3. Regularly check the lower supports or intermediate bearing bushings, seals, and replace them if they are worn or damaged.
4. Clean the accumulated materials in the spiral groove to prevent blockage and overloading. Inspect and maintain the electrical system to ensure safe operation.
3. Log Washer
The log washer is ideally suited for washing ore with high mud content and sticky materials.
The log washer cleans ore by breaking up mud with propeller blades fixed to a rotating shaft within a trough. Ore is fed in, and the blades’ action separates mud, which is discharged through an overflow, while the clean ore is pushed to the discharge port. This completes the washing process.
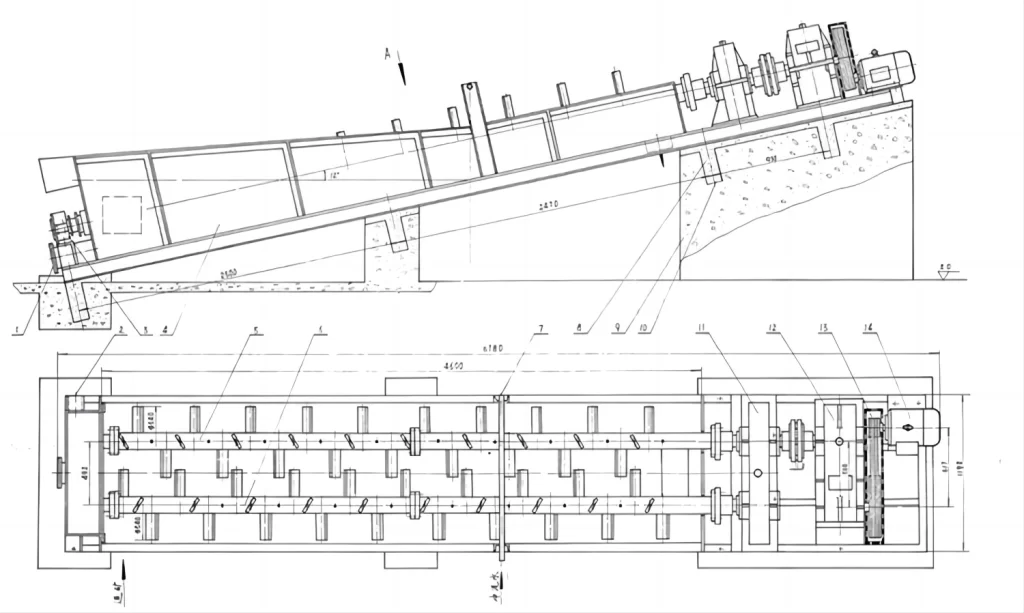
Operation Requirements:
1. Adjust the speed to match the specific material and cleaning requirements.
2. Monitor water quality to prevent equipment blockages or accelerated wear due to impurities.
3. Maintain the correct installation angle to ensure proper material flow.
Maintenance Requirements:
1. Clean the trough interior to prevent deposits from affecting the washing efficiency.
2. Perform thorough visual inspections and keep records of parts such as the reduction gearbox, flange joint surfaces, bearing covers, shafts, bearings, and reduction gears.
3. Weld or replace parts with fine cracks, scratches, or other imperfections on the reduction gearbox or flange joint surfaces.
4. Regularly check the condition of components like blades, rolling bearings, reduction gears, and coupling pins and holes, replacing them promptly when necessary.
4. Vibrating Washing Screen
The vibrating washing screen is not a professional ore washer. It combines the actions of screening and washing to clean ore with low mud content. Ore is fed onto a vibrating screen with multiple water spray pipes. The vibration of the screen causes the ore to move across the screen surface, while water sprays clean the ore.
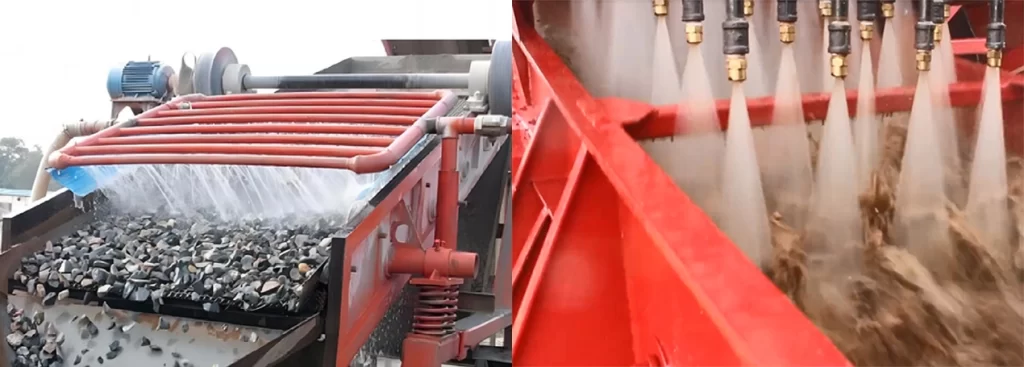
Operation Requirements:
1. Adjust the vibration frequency and screen size according to the ore size and clay content.
2. Ensure the screen is clean and intact to prevent a decrease in washing efficiency due to damage.
3. Optimize screening and washing by adjusting the vibration frequency and amplitude as needed.
Maintenance Requirements:
Regularly inspect the screen, springs, and bearings of the vibrating screen and replace them when worn to maintain efficiency.
Lubricate the bearings and other moving parts to reduce friction and wear.
Check the spray pipelines for leaks or blockages to maintain optimal performance.
Conclusion of Ore Washer Maintenance
All stone and ore washing machines, including spiral washers, required regular maintenance and inspection to ensure normal operation and production efficiency. Operators should receive proper training to understand the correct operation methods and safety procedures. Additionally, a regular maintenance plan should be formulated, including lubrication, replacement of worn parts, and inspection of electrical systems, to extend the service life of the equipment and ensure safe operation.
FORUI Machinery customizes the most suitable ore washing equipments based on your specific needs and mineral characteristics, providing efficient, reliable, and environmentally friendly ore cleaning solutions.
If you don’t know how to choose ore washers, contact us.
Henan Forui Machinery Technology Co.,Ltd
Email: kathy.niu@foruimining.com
support@foruimining.com
WhatsApp: +8618838083794
Your reliable mineral processing expert.
- How to Chose the Efficient Ore Washing Machine
- HOW DOES TROMMEL SCRUBBER WASH ORE?
- HOW TO CLEAN THE ORE WITH LARGE MUD CONTENT? LOG WASHER
- What Equipment Do We Use To Wash Fine Material? Spiral Washer