Chromite Overview
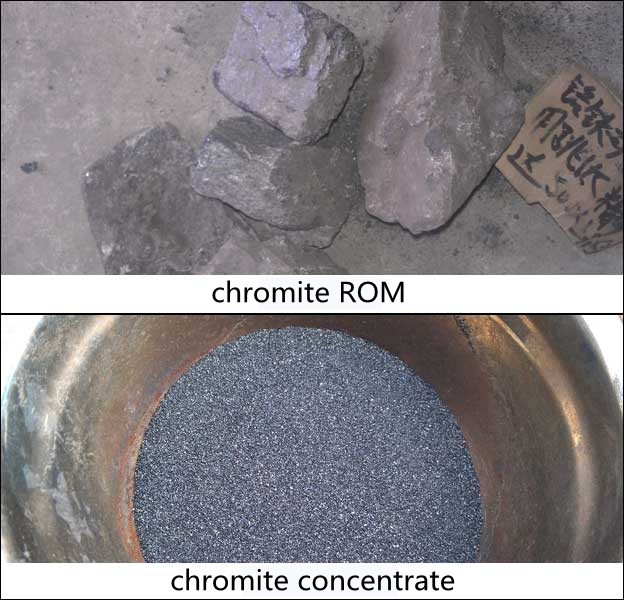
In the metallurgical industry, chromite is mainly used to produce ferrochrome and metallic chromium. As an additive to steel, ferrochrome alloy can produce a variety of special steels with high strength, corrosion resistance, wear resistance, high-temperature resistance, and oxidation resistance. Chromite is a mineral resource in short supply, with few reserves and low output. In industry, minerals such as ferrochromium, chromium spinel, chromium-rich spinel, and hard chromium spinel are often collectively referred to as chromite.
Chromite is dark brown to iron black, brown, with metallic luster and opaque. The hardness is 5.5, the relative density is 4.4-5.1, and it has weak magnetic properties. Mainly produced in ultramafic rocks, symbiosis with olivine, orthopyroxene, chromium garnet, spinel, titanomagnetite, platinum group minerals, etc. It is produced in disseminated, lenticular, strip-shaped, bean-shaped, and dense lumps.
Chromite ore Beneficiation Process
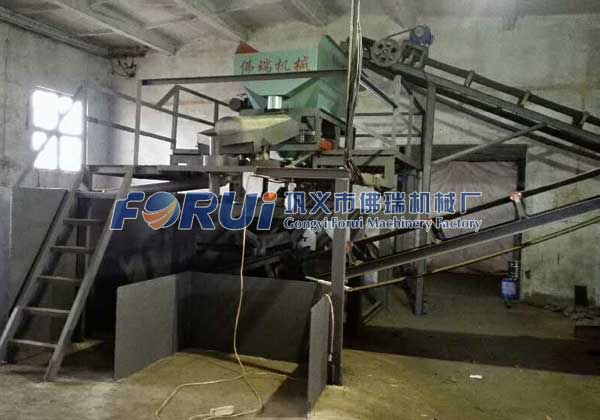
From the physical properties of chromite ore, it can be known that the embedded particle size of chromite ore is medium to fine particle size. The difference in specific gravity between the useful minerals of chromite and the associated gangue is very obvious, and gravity beneficiation is suitable. In fact, in the industrial application of chromite beneficiation, gravity beneficiation is the most widely used. Let me share with you the gravity beneficiation process of chromite ore.
Preprocessing Stage
The raw chromite ore is coarsely crushed by the jaw crusher and then enters the circular vibrating screen for screening. After screening, the materials larger than 30mm enter the fine jaw crusher for secondary crushing, and the materials smaller than 30mm are crushed with the fine jaw crusher. The materials are mixed into the silo of the rod mill. Through the vibrating feeder, the material is evenly fed into the rod mill for rough grinding. The purpose of rough grinding is to break the contiguous body of ore to ensure the smooth progress of the subsequent gravity beneficiation process.
Beneficiation Stage
The gravity beneficiation process uses jigs and jigs to beneficiate the chromite ore. The final concentrate is directly produced in the process, and the tailings enter the magnetic separation process for sweeping. The magnetic separation process is designed to recover the chromite that cannot be recovered by the jig because of the undissociation of the monomer. The concentrate recovered by the magnetic separation enters the ball mill for grinding, and then enters the shaker gravity beneficiation process after the monomer dissociation degree is increased to obtain the final concentrate and tailings.
The treatment process for the tailings of the jig machine is determined according to the recovery rate required by the customer. The recovery rate of the jig machine is generally around 85%-90%. If the customer has strict requirements on the recovery rate of the chromite ore, the jigging machine tailings must be treated.
The chromite beneficiation process adopts the combined process of gravity beneficiation-magnetic separation-gravity beneficiation to beneficiate and purify the chromite ore, and the recovery rate and concentrates grade of the beneficiation can meet the ideal requirements. Therefore, it is widely used in the field of chromite beneficiation, and it is a very effective chromite beneficiation process.
Alluvial Chromite Beneficiation
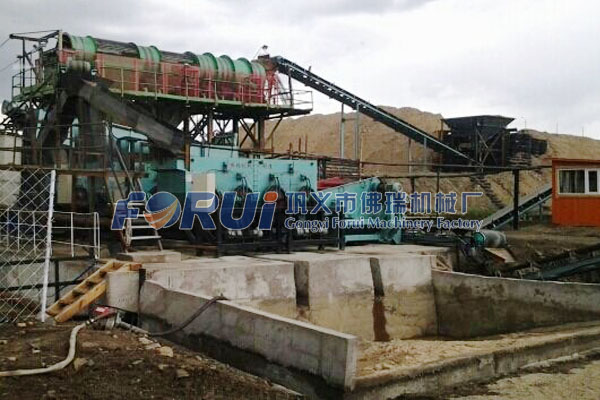
Chromite has not only rock ore but also placer. Fore Machinery once provided a complete set of beneficiation equipment for the chromite placer ore of the Philippines customer. Generally, the content of the soil in chromite placer is relatively large, and its grade can be significantly improved after washing the ore through the spiral washing machine. Then the ore beneficiation is carried out by the jig of the gravity beneficiation equipment, and the waste rock is separated out. The grade of the chromite ore can easily meet the expected requirements. The customer’s raw ore grade is around 4.8%. Previously, high-pressure water gun washing was used for beneficiation, and the grade can reach 25%. It can be seen that the customer’s alluvial chromite contains a large amount of soil. The use of high-pressure water guns to wash the beneficiation has a low recovery rate and processing capacity. In order to improve the recovery rate and processing capacity, the customer entrusted the technicians of Forui Machinery to provide it with a more reasonable beneficiation process and equipment configuration.
Magnetic Separation of Chromite
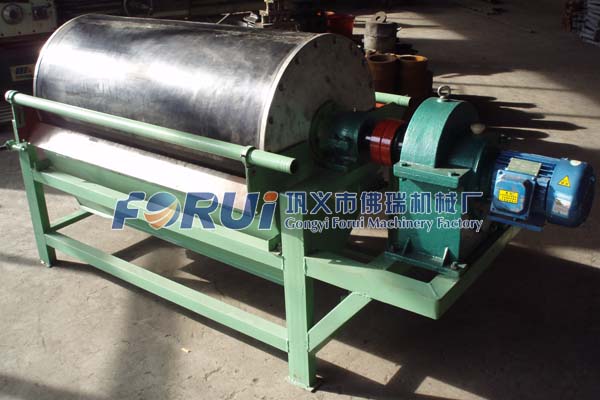
Gravity beneficiation has the advantages of high efficiency, energy saving, environmental protection, and low investment in chromite beneficiation. However, this kind of beneficiation technology cannot be used in water-scarce areas, because the gravity beneficiation method requires water as a medium to separate useful minerals and waste rocks. Since chromite has a certain magnetic permeability, but waste rock does not, the magnetic separation method can also be used to effectively purify chromite. Although the magnetic separation method can be used to purify chromite ore, the investment in magnetic separation equipment is relatively large, and the grade of chromite ore concentrate by magnetic separation method is generally not high, so the domestic chromite ore beneficiation generally adopts the gravity beneficiation Method and gravity beneficiation equipment.
Chromite Gravity Beneficiation Equipment
Gongyi Forui Machinery Factory, founded in 1986. We are one of the leading suppliers of beneficiation equipment in Asia. We can design and manufacture professional chromite processing equipment for you. Welcome to visit our company. We are dedicated to serving you! If you need equipment quotation and process flow, please feel free to Contact Us:
- Whatsapp: +8618026978087
- Email: asa.guo@foruimining.com