Barite processing is essential for obtaining high-grade barite (BaSO4), a sulfate mineral widely used in drilling fluids, fillers, and white pigments. Typically found with sulfide minerals like galena (PbS) and sphalerite (ZnS), hydrothermal barite ore must be processed to remove these impurities and ensure its industrial quality.
1. Barite Beneficiation Method
There are several types of barite ores, and the beneficiation methods used vary accordingly, as shown in Table 1. Among them, gravity separation, magnetic separation and flotation are the most commonly used methods. Color separation is also gradually applied to the screening of high-quality barite
1.1 Gravity Separation:
Gravity separation is suitable for barite ores with coarse particle size and significant density differences. Common equipment includes jigs and shaking tables. Brief Introduction of Barite Gravity Beneficiation Process
1.2 Magnetic Separation:
Magnetic separation is suitable for barite ores associated with magnetic minerals such as magnetite and pyrite.
1.3 Flotation:
Flotation is suitable for barite ores with fine particle size and small density differences. Flotation is currently the most widely used method for barite beneficiation.
Beneficiation Method | Principle | Application |
Manual Selection | Differences in color between barite and associated minerals | Selecting lump barite |
Gravity Separation | Density difference between barite and associated minerals | Residual-type deposits |
Flotation | Differences in the surface physicochemical properties of barite and associated minerals | Commonly used for sedimentary barite deposits and hydrothermal barite deposits associated with sulfide minerals and fluorite |
Magnetic Separation | Magnetic difference between barite and iron oxide minerals | Mainly used to remove iron oxide impurities |
Chemical Refining | Differences in the chemical properties of barite and associated minerals | Used to remove impurities such as carbon, iron, manganese, vanadium, and nickel |
Mineral Color Separation | Differences in color between barite and associated minerals | Select white barite and remove dark stones |
2. Flotation for Barite-sulfide Mineral Mixed Ore
Hydrothermal barite ore often contains associated minerals such as galena (lead), sphalerite (zinc), and fluorite. Due to the different surface properties of these minerals, a multi-stage flotation process can be used in barite processing to separate them. The typical sequence is to first float galena (lead) and sphalerite (zinc), then barite, and finally fluorite. This sequence is adopted because:
2.1 Preferential Flotation of Sulfide Minerals:
Galena and sphalerite have better floatability. Their flotation reagents (e.g., xanthate and dithiophosphate) can preferentially float sulfide minerals while suppressing non-sulfide minerals like barite and fluorite.
2.2 Minimizing Reagent Interference:
After floating galena and sphalerite, the flotation reagents’ interference is minimized, providing a cleaner environment for subsequent barite and fluorite flotation.
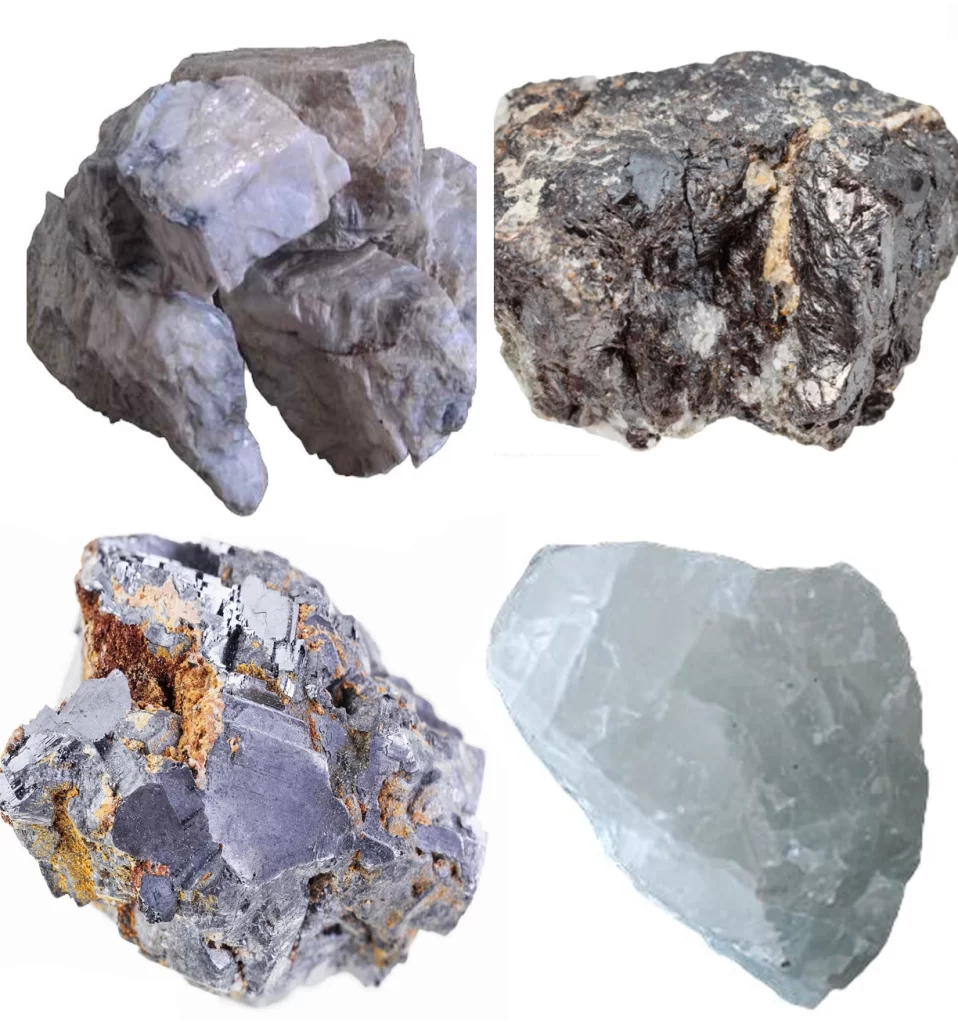
3. Flotation Process of Barite-Galena-Sphalerite-Fluorite Mixed Ore
3.1 Crushing and Grinding
Initially, crush and grind the ore to achieve a suitable particle size for flotation, typically to 75 microns.
3.2 Flotation of Galena
To begin the flotation process, adjust the pulp pH to neutral or slightly alkaline (pH 7-8). Add sulfide mineral collectors, such as xanthate, and frothers to float galena.
Collect the galena concentrate, and move the tailings to the next stage.
3.3 Flotation of Sphalerite
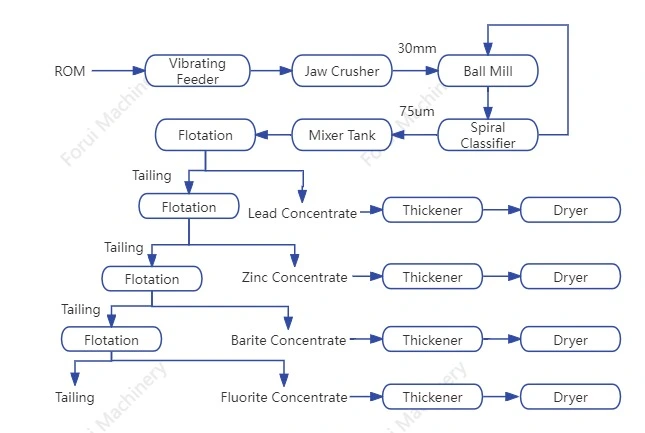
Adjust the pulp pH to alkaline (pH around 9-10). Add sphalerite collectors, such as xanthate, and activators like copper sulfate. Collect the sphalerite concentrate, and direct the tailings to the next stage.
3.4 Flotation of Barite
During barite processing, adjust the pulp pH to neutral or slightly alkaline (pH 7-8). Add barite collectors, such as fatty acid collectors, to float barite. Collect the barite concentrate, and proceed with the tailings to the final stage.
3.5 Flotation of Fluorite
Adjust the pulp pH to alkaline (pH 9-10) to float fluorite. Add fluorite collectors, such as fatty acid collectors, and regulators like aluminum sulfate. Collect the fluorite concentrate and dispose of the remaining tailings.
3.6 Dewatering of Flotation Concentrates
After the flotation process, the concentrates from each stage—galena, sphalerite, barite, and fluorite—undergo dewatering to remove excess water and prepare them for further processing or sale.
4. Key Equipment for the Barite Flotation Process
Barite flotation equipment Products
- Jaw Crusher: For initial ore crushing.
- Ball Mill: For grinding the ore to the required fineness.
- Spiral Classifier: For classifying the ground ore.
- Mixing Tank: For preparing the ore pulp.
- Flotation Machine: For conducting the flotation process.
- Dewatering Equipment: For removing moisture from the final concentrates.
- Conveying Equipment: For transporting materials between stages.
Expertise in Barite Processing
FORUI Machinery specializes in the development and production of beneficiation equipment. With extensive experience in barite processing, we can design appropriate beneficiation processes based on your ore type, raw material characteristics, mine scale, and intended use. We provide professional beneficiation equipment and technical services to help you improve the efficiency and benefits of barite processing.
If you need equipment quotation and process flow, please feel free to Contact Us.
- WhatsApp: +8618838083794
- Email: Kathy.niu@foruiming.com
- Email: support@foruimining.com