1. Barite-fluorite Ore Flotation Process
Barite-type fluorite ores primarily contain barite as a gangue mineral (usually 10-40%) and are often associated with minor sulfide minerals (pyrite, galena, sphalerite), with some deposits containing a higher quartz content. Given the similar floatability of barite and fluorite, a flotation process involving the preferential bulk flotation of fluorite and barite, followed by separation, is commonly employed. During bulk flotation, oleic acid is generally used as a collector, and sodium silicate is used as a depressant to inhibit other gangue minerals.
Two main approaches can be adopted to separate the mixed fluorite-barite concentrate: depressing barite to float fluorite, or depressing fluorite to float barite.
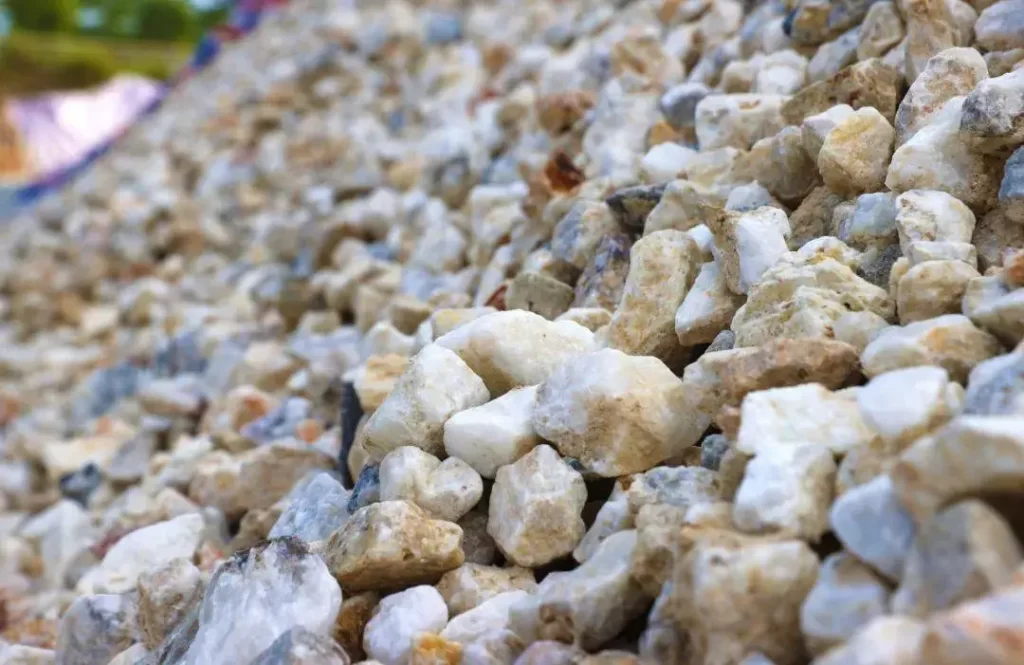
2. Depressing Barite to Float Fluorite
Common barite depressants include organic depressants (starch, dextrin, tannin, tannic acid) and FeCl₃. Oleic acid is used as a fluorite collector to preferentially float fluorite, followed by the recovery of barite from the tailings. This method is widely used.
Case Study:
Professor Shi Wentao processed a barite-type fluorite ore, which included 15% CaF₂ and 48% barite, by utilizing sodium oleate as a collector. He also employed sodium silicate, aluminum sulfate, and tannic acid as depressants. By conducting a flotation regimen consisting of one roughing stage followed by five cleaning stages, he managed to selectively float the fluorite from the mixed concentrate. This method led to the production of a fluorite concentrate that achieved a grade of 95.52% CaF₂, along with a recovery rate of 92.13%.
3. Depressing Fluorite to Float Barite
Sodium hydroxide and sodium silicate are often used to depress fluorite, and alkyl sulfates are used as collectors to float barite concentrate. Fluorite concentrate is then recovered from the tailings using sodium silicate as a depressant and sodium oleate as a collector. However, the grade or recovery rate of the obtained fluorite concentrate is often low.
Case Study:
Professor Li Mingfeng treated a barite-type fluorite ore containing 37.79% CaF₂ and 49.80% barite. After bulk flotation, a mixed fluorite-barite concentrate was obtained. Barite was then floated through a process of “1 rougher and 4 cleaners,” and fluorite was recovered from the tailings through a process of “1 rougher and 3 cleaners.” The obtained fluorite concentrate had a CaF₂ grade of 95.24% and a recovery rate of 81.04%, indicating a relatively low recovery rate.
4. Conclusion
In conclusion, for barite-type fluorite ores, the “preferential bulk flotation and depression of barite to float fluorite” approach is more favorable for improving the flotation indices of fluorite concentrate.
The flotation process and reagent selection for fluorite ore require experimentation to determine. The flotation treatment line for fluorite ore also varies and needs to be designed based on the mineral properties.
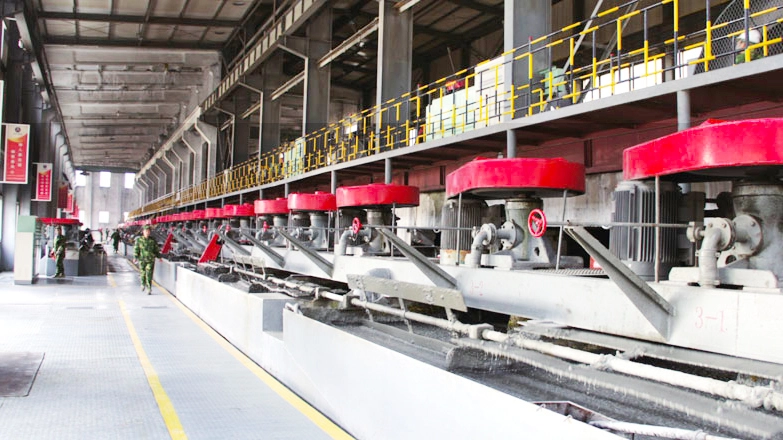
Forui Machinery Factory is a professional manufacturer of beneficiation equipment. Our factory has designed fluorite beneficiation technology and equipment configuration for multiple fluorite beneficiation plants and has a complete test platform. It can conduct beneficiation tests and design processes for customers.
Kathy Niu
Email: Kathy.niu@foruimining.com
support@foruimining.com
WhatsApp: +8618838083794
Henan Forui Machinery Technology Co.,Ltd
What is the Beneficiation Process of Fluorite Ore
Fluorite Flotation 01:Sulfide-Fluorite Ore Flotation
What Methods and Equipment Should be Used to Improve the Grade of Fluorite
Can the Low-grade Fluorite be Enriched by Gravity Beneficiation?
How to Improve the Grade of Fluorite by Using Gravity Dressing Process