1. Introduction to Barite
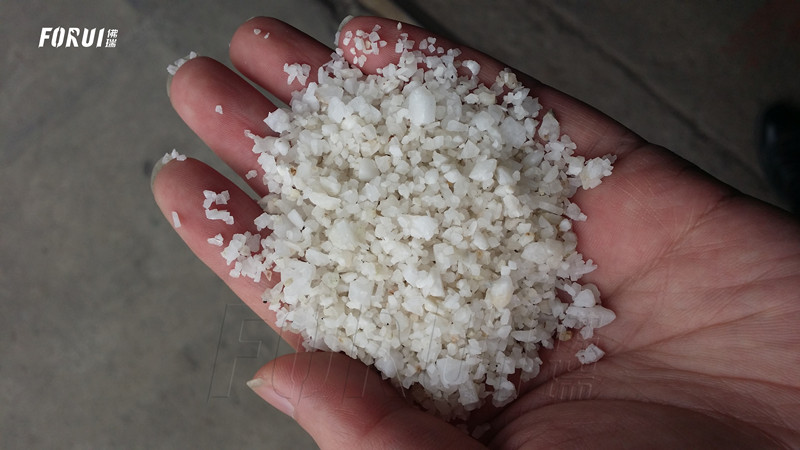
Barite is a common mineral of barium, and its main component is barium sulfate (BaSO4). Produced in low-temperature hydrothermal veins, such as quartz-barite veins, fluorite-barite veins, etc. Barite is often symbiosis with galena, sphalerite, chalcopyrite, cinnabar, etc. Barite can also be produced in sedimentary rocks, appearing in the form of nodules, mostly in sedimentary manganese deposits and argillaceous and sandy sedimentary rocks in shallow seas. In the residual clay covering layer of the weathered residual deposits, it often forms agglomerates and blocks.
The main purpose of barite:
- In oil drilling, it is mainly used as a weighting agent to cool the drill bit, take away the cutting debris, lubricate the drill pipe, close the hole wall, control the oil and gas pressure, and prevent the oil well from spontaneous blowout.
- In the chemical industry, it is mainly used to produce various barium compounds such as barium carbonate, barium chloride, barium sulfate, lithopone, barium hydroxide, and barium oxide. These barium compounds are widely used in reagents, catalysts, sugar refining, textiles, fire protection, various fireworks, synthetic rubber coagulants, plastics, insecticides, steel surface quenching, phosphors, fluorescent lamps, solders, grease additives, etc. .
- Used in glass deoxidizer, clarifier, fluxing agent, it can increase the optical stability, gloss and strength of glass.
2. Brief introduction of barite beneficiation method
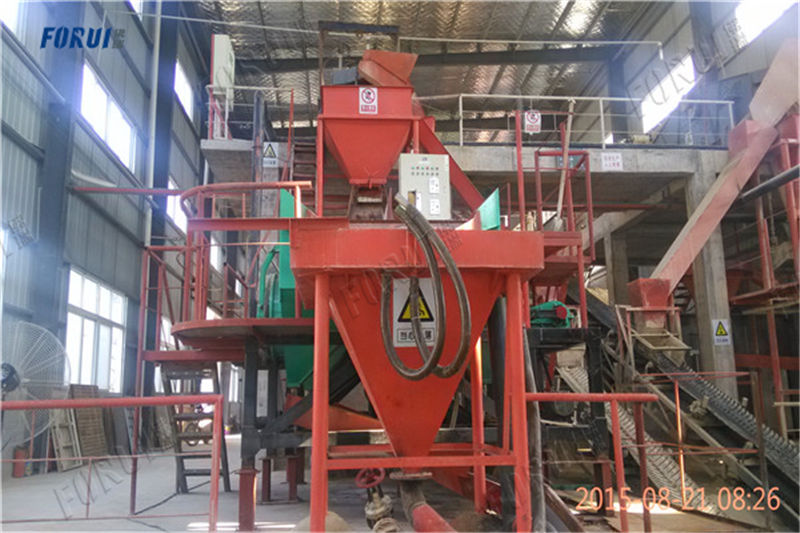
As a kind of mineral resource, barite mostly needs to be processed by ore beneficiation before it can be used in various industries. The beneficiation methods of barite ore are mainly divided into two types: gravity beneficiation and flotation.
1. Gravity beneficiation
The gravity beneficiation method is mainly based on the large difference between the specific gravity of barite and the associated gangue, and the gravity beneficiation equipment is used to separate minerals with different specific gravities. To obtain barite concentrates with a larger specific gravity and barite tailings with a smaller specific gravity, the equipment used is mainly a jig.
Because the gravity beneficiation method is based on the difference in specific gravity, and the beneficiation efficiency of fine-grained barite ore is not good, the gravity beneficiation method is only suitable for the beneficiation of coarse-grained crystals and minerals with a certain specific gravity difference with the associated gangue, such as fluorite -Barite ore, quartz-barite ore and other types of barite ore.
2. Flotation
The flotation method for barite ore selection is mainly based on the difference in floatability between minerals. It has excellent beneficiation effects for fluorite-barite ore and calcite-barite ore. The equipment used includes crushers, ball mills, classifiers, flotation machines, etc.
Since the flotation method requires the particle size of the ore to be within the suitable flotation particle size range, and the particle size of the flotation is mostly between 80-200 mesh, so the flotation is only used for the processing of fine-grained low-grade barite beneficiation. It is suitable for the flotation separation of barite-calcite with little difference in specific gravity.
3. Brief introduction of barite beneficiation equipment
Barite beneficiation equipment is divided into gravity beneficiation equipment and flotation equipment. Gravity beneficiation equipment mainly refers to jigs, and flotation equipment is flotation machine. Both of these two main sorting equipment need to use crushers, vibrating screens, Auxiliary equipment such as conveyors, ball mills, classifiers and mixing barrels are also used in flotation.
Barite gravity separation equipment mainly adopts crushers, conveyors, and jigs to complete the processing of ore separation, and its beneficiation cost and equipment investment are relatively low, while barite flotation equipment uses crushers, conveying Machines, ball mills, classifiers, mixing tanks, flotation machines and other equipment have relatively large operating costs and equipment investment. The barite ore in many provinces and regions in my country is a coarse-grained barite rich ore. Good mineral processing indexes can be obtained through simple gravity beneficiation. Therefore, the application of gravity beneficiation equipment in the field of barite beneficiation is extremely common. However, due to environmental protection requirements, equipment investment and operating costs, flotation equipment has gradually withdrawn from the field of barite beneficiation and replaced by gravity beneficiation equipment.
4. Introduction to the process flow of 80 tons of barite beneficiation per hour
Gongyi Forui Machinery Factory is a professional mining jig machine manufacturer. Since its establishment, it has successively established multiple barite gravity beneficiation production lines in Panzhihua, Chongqing, Guiyang, Jinchang, Anshan, Mianchi, Jingmen and other places in my country. , The customer’s response is good. Our factory has rich experience and unique insights on the gravity separation of barite ore. According to our factory’s years of experience in the field of barite gravity beneficiation, we designed 80 tons of barite for Hubei customers. The process of beneficiation in Gongyi, the details are as follows:
4.1. Process flow chart of barite beneficiation
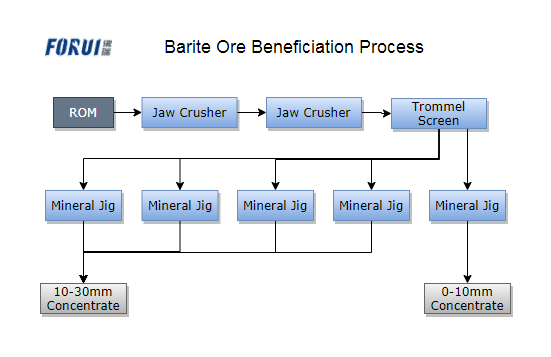
4.2. Brief introduction of barite beneficiation process
The beneficiation process is a gravity beneficiation process, and a jig machine is used as the main equipment for the separation and purification of barite ore. The process flow is described in detail below.
①Breaking process
Barite is brittle and fragile, so the crushing process mainly adopts a simple and practical jaw crusher. A two-stage crushing process is used to crush the large barite that is mined to reach the effective size range of the jig machine. It is recommended to use PE400600 jaw crusher for the first stage of crushing, and PEF2501000 fine jaw crusher for the second stage of crushing.
After one stage of crushing, the product is conveyed to the second stage fine-jaw crusher through a belt conveyor to be crushed again to meet the selected particle size requirements of the subsequent sorting equipment. Since the customer requires no dust in the production process, it is recommended to add water appropriately in the crushing process to reduce the dust generated when the crusher is working.
②Screening process
Jigging machine sorting has strict requirements on the size of the material. Generally, classification is required to achieve better beneficiation indicators and higher processing capacity. Therefore, a screening process is required in the gravity beneficiation process of barite. After screening, the crushed products are divided into different grades and enter the jigging machine for jig separation.
The screening process adopts a simple and practical circular vibrating screen with large processing capacity, high screening efficiency, low failure rate, large processing capacity, high screening efficiency, and easy operation. It is an ideal equipment for barite ore screening . Since the screening process will also produce a certain amount of dust, it is recommended to also set up water supplement in this process to reduce the generation of dust.
③Buffering process
When the jig machine is working normally, it needs a uniform and stable amount of ore. Therefore, it is best to set up buffering mechanisms and equipment before the jig machine, such as a silo and a vibrating feeder. The role of the silo is to avoid the work of the previous equipment The amount fluctuates from large to small, and there is a certain amount of material in a moderate amount. The function of the vibrating feeder is to feed the jig material uniformly and stably. The existence of these two auxiliary equipment is crucial to the normal and efficient work of the subsequent jig machine. Important role.
①-④ No. silo uses 15m³ silo, ⑤ No. silo uses 25m³ silo, in order to facilitate transportation, the silo designed and produced by our factory is a combined detachable silo. The vibrating feeder adopts GZ3 electromagnetic vibrating feeder.
④Jig sorting process
According to customer requirements, we use two types of jigs to sort the crushed barite materials. Since fine-grained materials are inevitably produced during the crushing process, it is recommended to use two types of jigs. Separate the coarse and fine materials. ①-④Jig machine adopts coarse-grain AM30 jigging machine, which is used to process 10-30mm coarse-grained barite ore. No. ⑤ jig machine adopts 2LTC-6109/8T jigging machine, which can handle 0-10mm fine-grained barite ore. Grain barite ore.
The concentrate produced by the ①-④ jig is fed into the 10-30mm granular concentrate pool through a pipeline or chute, and the concentrate produced by the No. ⑤ jig is collected into the 0-10mm granular concentrate pool. All the tailings produced by the jigs are collected into the tailings pond and transported away by forklifts or conveyors after precipitation.
⑤Dehydration process
Since the customer requires mechanical dehydration, the simplest precipitation and flat dehydration process can be used for the dehydration process. The mechanical dehydration scheme can also be designed according to the requirements.
⑥Water circulation process
The jigger consumes a lot of water and generally uses circulating water. Therefore, it is necessary to design a water circulation plan according to the specific conditions of the customer’s site to ensure the normal and effective process of the process.
5. 80 tons of barite related equipment configuration when processing
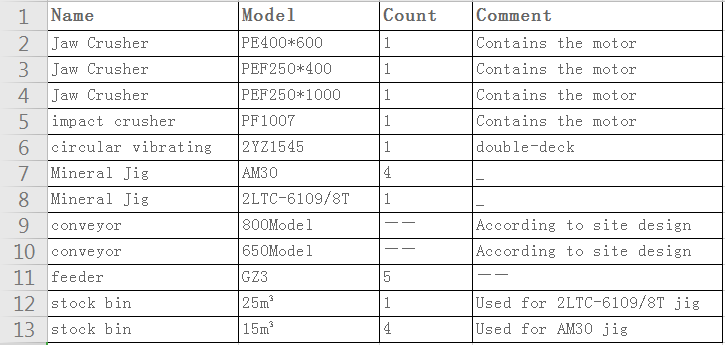
6. The principle and process of selecting barite by jig machine
The principle of selecting barite by the jig is based on the specific gravity difference between the barite and its associated gangue, and the barite with a larger specific gravity is stratified by the specific gravity in the vertical alternating current generated by the jig’s agitation. The sedimentation speed in the vertical alternating water flow is faster, and it is located in the lower layer of the sorting tank of the jig machine, while the gangue minerals with a smaller specific gravity occupy the upper layer of the sorting tank, and are discharged out of the machine through a special discharge device to obtain the specific gravity. Two minerals of different sizes, namely concentrates and tailings.
The barite ore is fed into the jig machine stably and evenly through the silo and feeder, and is stratified according to the density in the alternating water flow generated by the jigging machine. The barite has a relatively large proportion and occupies during the stratification process. In the lower space of the sorting tank, the specific gravity of the gangue is relatively small, and it occupies the upper space during the stratification process. The two materials with different specific gravities are discharged separately through a special distribution device to obtain two materials with different specific gravities. Spar concentrates and tailings.
7. Barite beneficiation cost accounting
The barite beneficiation process is a gravity beneficiation process, which has the characteristics of energy saving, high efficiency, and environmental protection. The following is the detailed content of barite beneficiation cost accounting:
7.1. Energy consumption cost
Electric equipment such as crushers, conveyors, vibrating screens, jigs, and vibrating feeders are used in this process. The power of the coarse jaw crusher is 37 kilowatts, the fine jaw crusher is 37 kilowatts, and the vibrating screen is 15 kilowatts, AM30 jig machine is 3 kilowatts, 2LTC-6109/8T jig machine is 6 kilowatts, conveyor 5.57=38.5 kilowatts, and the water pump is 305=150 kilowatts, the actual total power consumption is 295.5 Kilowatts, add the power of the intermediate water replenishment process, the total power is between 290-310 kW, calculated at 1 RMB per kilowatt-hour of electricity, the total power consumption of the total process flow is about 300 degrees per hour, and the energy consumption cost is less than 300 RMB.
7.2. Labor cost
The process adopts automatic operation and management, so the number of labor required is limited. Under normal circumstances, only 2-3 people are required. 1-2 people are responsible for the normal operation and operation and maintenance of the equipment, and another person is responsible for the feeding of the loader. Based on 150 RMB per person per day, the labor cost is between 450-500 RMB.
7.3. Loader use cost
The loader is responsible for the feeding link of the process. According to experience, the loss (fuel consumption) of the loader per hour is about 75 RMB, and the mechanical loss is negligible.
7.4. Calculation of the total cost of barite beneficiation
The cost of selecting a ton of barite ore = (electricity fee + labor cost + loader cost) / 80 tons = (300 + 500 + 75) / 80 = 875/80 = 10.9375 RMB.
It can be seen that the cost of using this process to sort barite ore is 10.9375 RMB per ton.
Gongyi Forui Machinery Factory is a professional ore dressing equipment manufacturer. The factory mainly produces jigs, magnetic separators, flotation machines, ball mills, classifiers, and other fluorite beneficiation equipment. At the same time, we will design the fluorite beneficiation process and equipment configuration for customers, and welcome customers to visit our factory for guidance. Contact number: +8618026978087.