The development and utilization of weakly magnetic iron ore usually require beneficiation processing, and different beneficiation processes are used according to the different disseminated particle sizes of iron minerals.
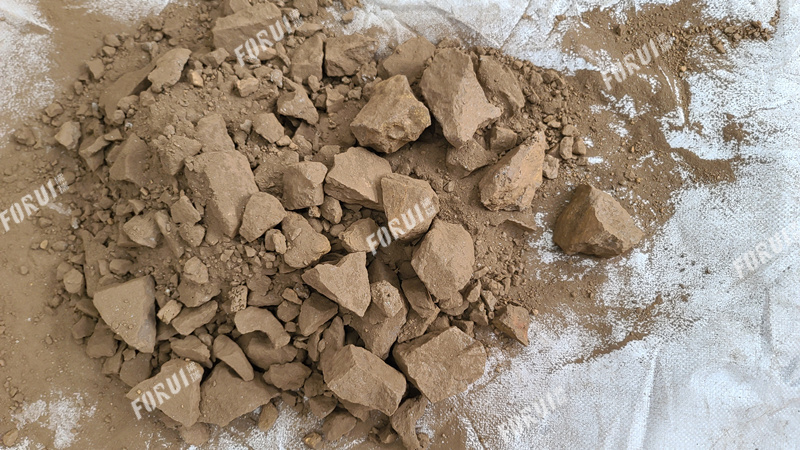
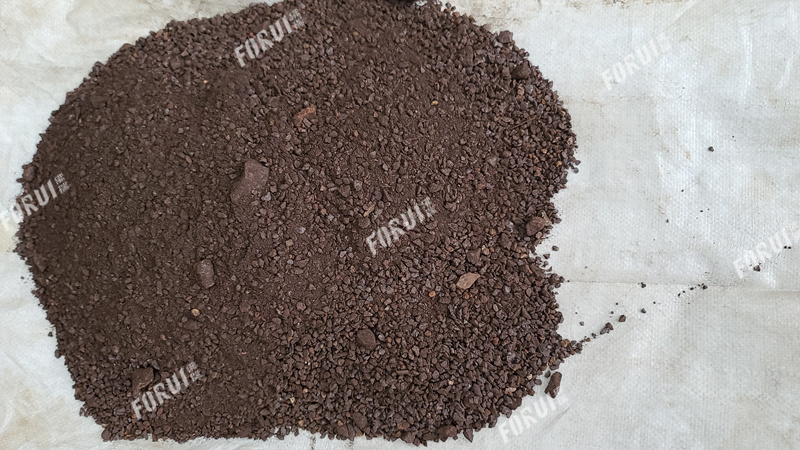
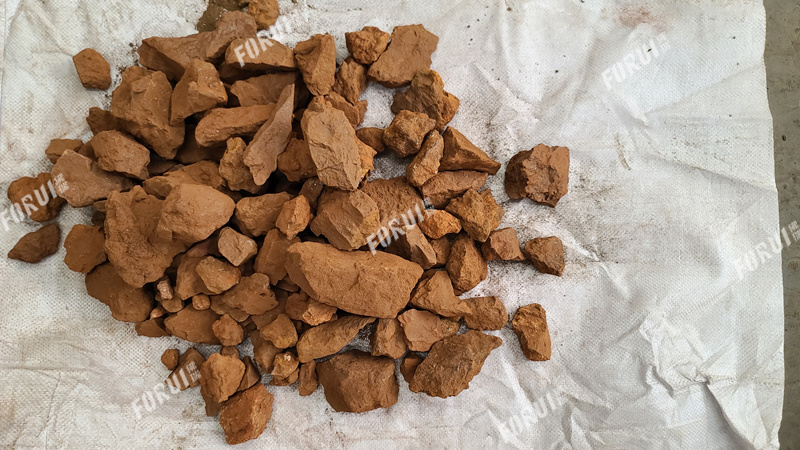
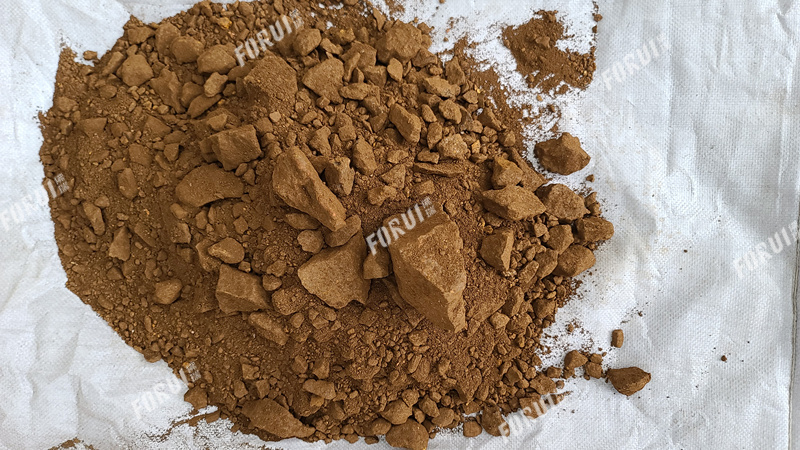
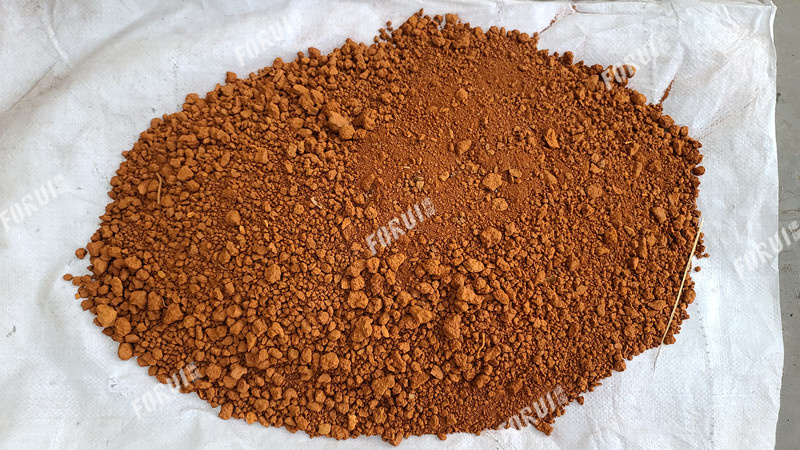
A. Coarse-grained Weakly Magnetic Iron Ore
Coarse-grained weakly magnetic ore refers to iron ore with a disseminated particle size of more than 2mm. It is mainly processed by two methods: gravity concentration and strong magnetic separation.
1. Gravity Concentration
Gravity concentration is an important method for processing weakly magnetic iron ore (coarse-grained rich hematite, false hematite, limonite, and siderite), mainly using jigging beneficiation and spiral separation. Because of its simple equipment, low cost, low power consumption, and no chemical reagents in production, it is widely used all around the world.
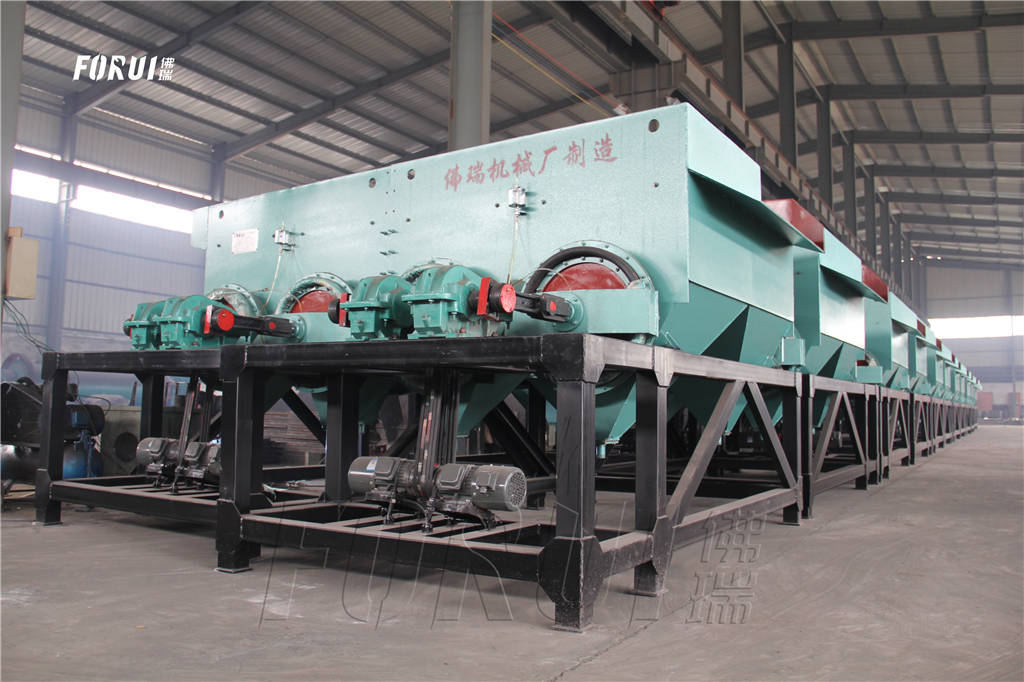
Jigging beneficiation refers to gravity separation operations carried out in a vertical alternating medium flow. The jig is a deep groove type of equipment, and there are many types of it. The eccentric link mechanism is used to push the rubber diaphragm to reciprocate so that the water flow produces up and down pulsating movement in the jigging chamber.
The sorting process is: the ore is fed to the sieve plate of the jig room to form a bed. When the water flow rises, the bed is pushed to loosen up, and the denser particles lag behind the less dense particles and stay relatively below. Then the water flow drops, the bed layer tends to be tight, and the heavy mineral particles enter the bottom layer first. After repeated loosening and compacting, the minerals are finally stratified according to density. After the lower and upper minerals are discharged separately, concentrates and tailings are obtained. Except for very fine raw materials, jig beneficiation can process ore of various particle sizes. As long as there is a sufficient density difference between the minerals. The equipment has a simple process operation and a large equipment processing capacity. It can obtain the final concentrate or the final tailings in a single separation and is widely used in the processing of coarse-grained and medium-grained ores.
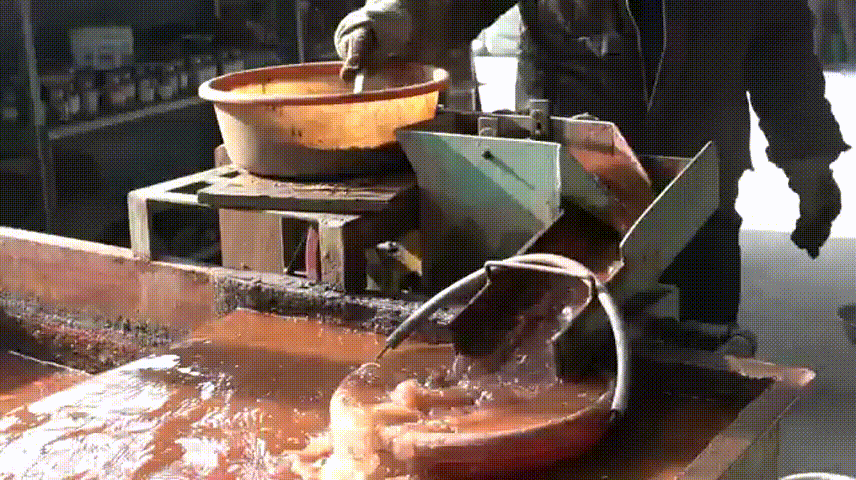
The spiral concentrator is a flowing film gravity separation equipment composed of a spiral trough with a vertical axis. The slurry flows in a rotary flow on this equipment, and the ore particles are subjected to the combined action of gravity, centrifugal force, friction force, and the combined force generated by the inclined water flow. , So that the mineral particles are separated according to the density along the radial direction of the trough.
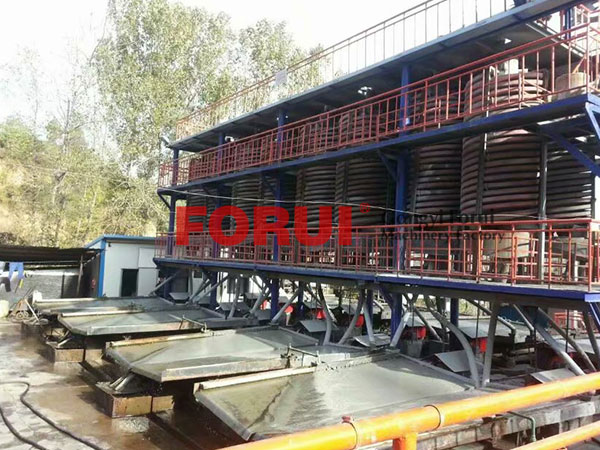
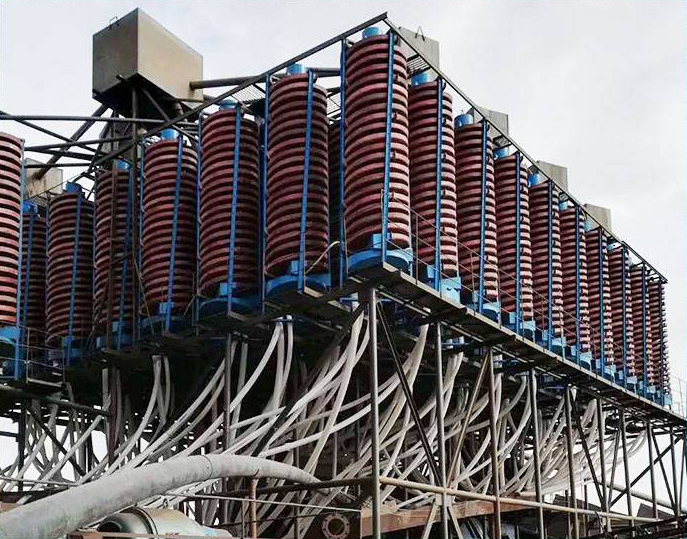
The spiral concentrator is suitable for processing alluvial placer deposits, especially for those with high dissociation of useful mineral monomers and flat shapes. For residual deposits with more contiguous bodies, the recovery rate is lower. In addition, for ores with high mud content, must be deslimed and classified before they can enter the spiral concentrator.
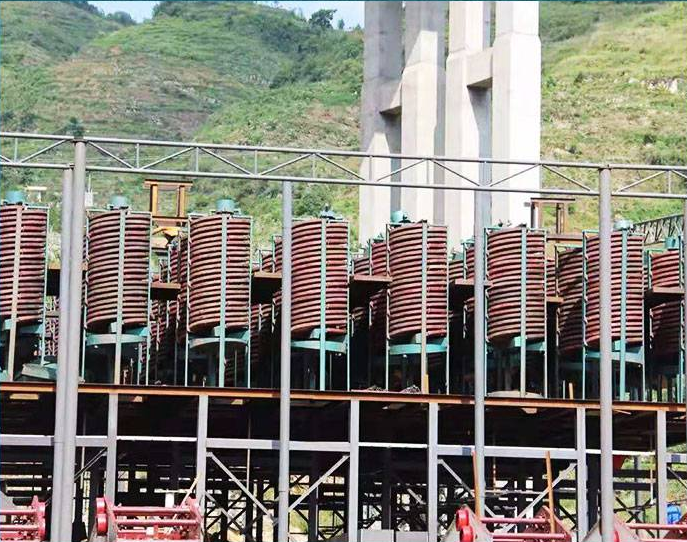
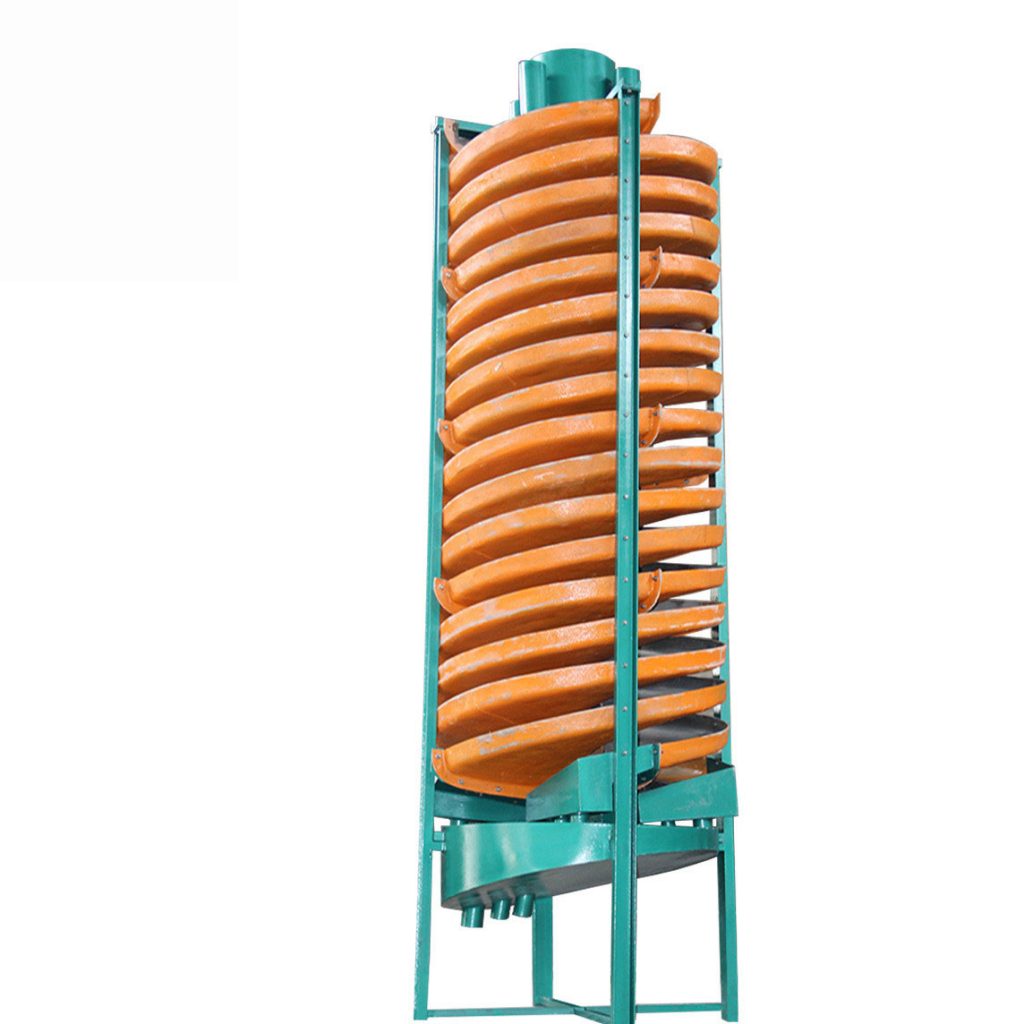
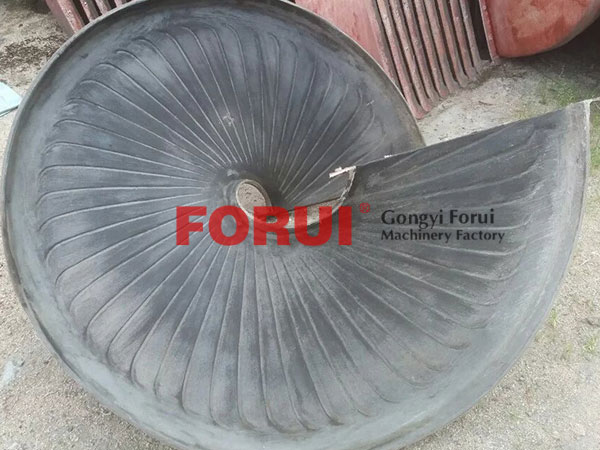
For example, the Fabrica iron ore of Fertco Minerals Company in Brazil is mainly composed of interlaced rock layers rich in iron and quartz. The main ore is hematite, and a small amount of magnetite, limonite, Al203, and P content is relatively high. The grade of iron ore is about 39%. After crushing and screening, it is divided into two levels of -8+1.5 mm and -1.5+0.1mm, -8+1.5mm is sent to the jig, and -1.5+0.1mm is sent to the spiral concentrator, The concentrate is selected by the jig machine and the spiral concentrator is mixed and stacked, and the final concentrate grade reaches 68%.
2. Strong Magnetic Separation
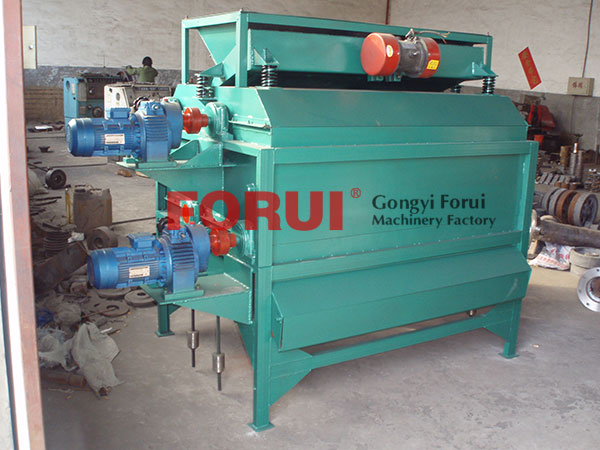
Magnetic separation is the most important method of iron ore beneficiation. Due to the existence of gangue intergrowth in large particles of weakly magnetic iron ore, there are almost no examples of obtaining the final concentrate only through strong magnetic separation.
Mines at home and abroad usually use strong magnetic separation for pretreatment: discarding a large number of tailings to reduce the workload of the next operation, so as to achieve the purpose of energy-saving and consumption reduction. There are also a few manufacturers that increase the grade of iron ore by 2 to 5% through strong magnetic separation and sell directly.
B. Medium-grained Weakly Magnetic Iron Ore
The disseminated grain size of this type of iron ore is 2~0.2mm. The processing methods mainly include gravity concentration, strong magnetic separation, gravity concentration-electric separation, roasting magnetic separation, and the combined process of multiple methods.
For example, the Kawei Iron Mine owned by Brazil’s Vale Company handles 31 million tons of ore each year, including 6 million tons of hematite and 25 million tons of ferrite, with an average iron content of 50%. The iron ore fines are divided into 3 grades, which are larger than 8mm, 8~1mm, and smaller than 1mm. Grain size larger than 8mm needs to be crushed again; 8~1mm particle size products are sent to jigging workshop for concentrating; Grain size smaller than 1mm is classified and deslimed by the hydro cyclone, and then separated by high field strength Jones type strong magnetic separator. The quality of the product is 66.8% iron.
C. Fine-grained and Micro Fine-grained Weakly Magnetic Iron Ore
The disseminated grain size of the fine-grained weakly magnetic iron ore is 0.2~0.030mm, and the disseminated grain size of the micro fine-grained weakly magnetic iron ore is generally below 0.030mm. Fine-grained and super fine-grained weakly magnetic iron ore is generally considered to be difficult to process iron ore. Relatively the beneficiation process is complicated and the processing cost is high. The methods for processing this type of iron ore include roasting-magnetic separation, flotation, gravity separation, strong magnetic separation, and a combined process of two or more beneficiation methods.
Gongyi Forui Machinery Factory is a high-quality enterprise specializing in the production of beneficiation equipment. Over the years, it has produced gravity beneficiation, magnetic separation, flotation, and other beneficiation equipment, and has accumulated a lot of practical experience. Forui Machinery is involved in lead-zinc ore, gold ore, fluorite, barite, pyrite, hematite, limonite, magnetite, manganese ore, antimony ore, tungsten ore, tin ore, celestite, etc. In the field of beneficiation of a variety of minerals, fruitful results have been achieved.
If you need equipment quotation and process flow, please feel free to Contact Us